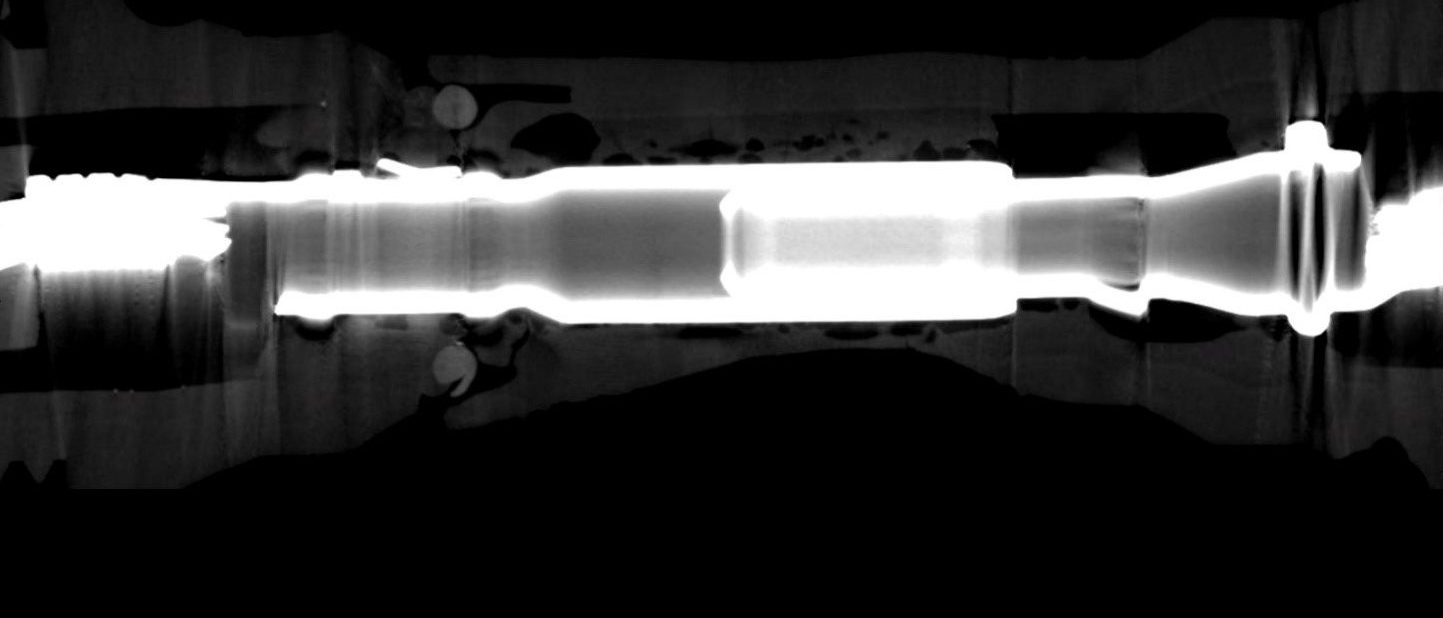
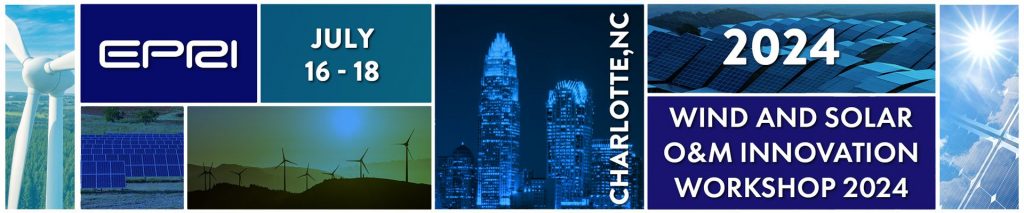
Sandia-EPRI hosted PV Connector Reliability Workshop presentations are now available!
Mission
To increase the robustness of the US solar infrastructure by identifying, quantifying and mitigating the risks posed by poorly-installed, mismatched and/or poorly designed and manufactured connectors.
Project Objectives
This DOE-funded project has three primary objectives, which are to:
1) Investigate and document the operational functionality of PV connectors in the US
2) Analyze degraded and failed connectors to identify failure mechanisms and root causes
3) Calculate the economic losses attributable to degraded and failed connectors
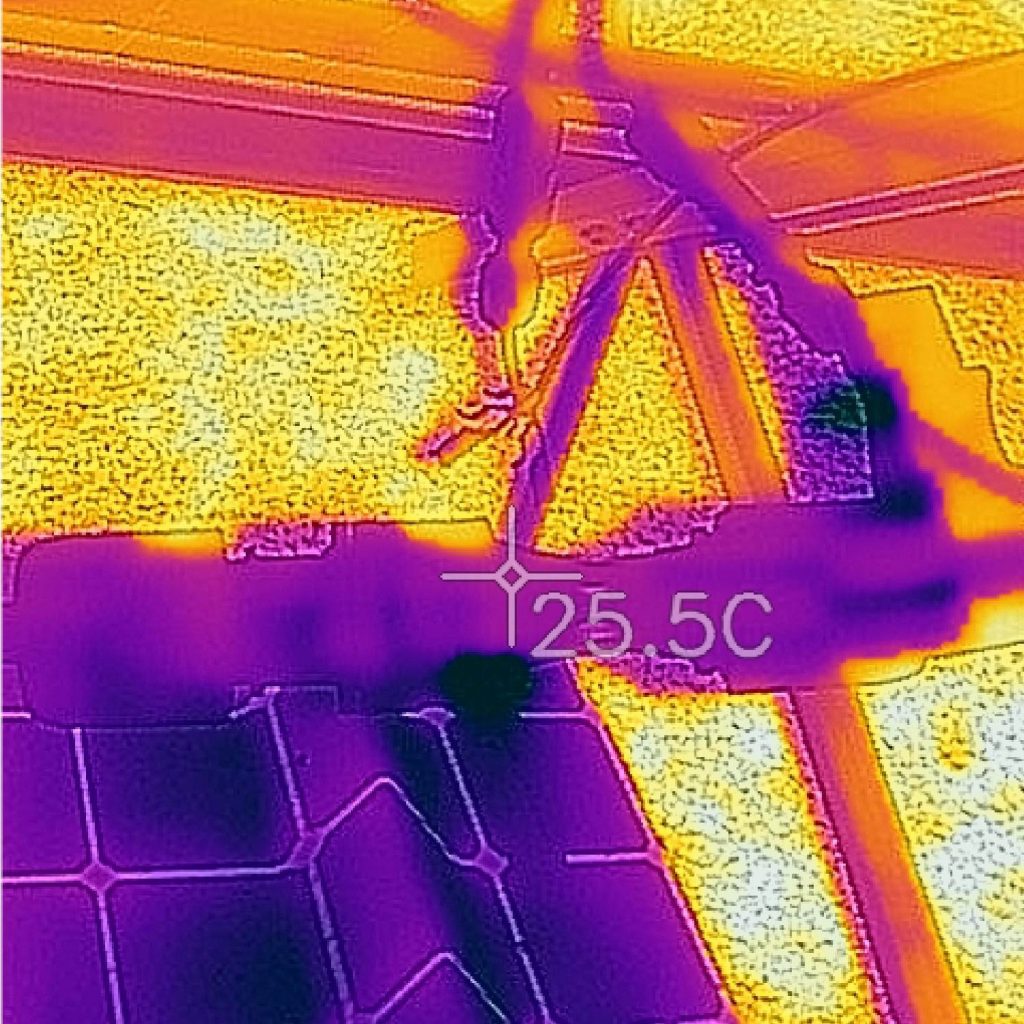

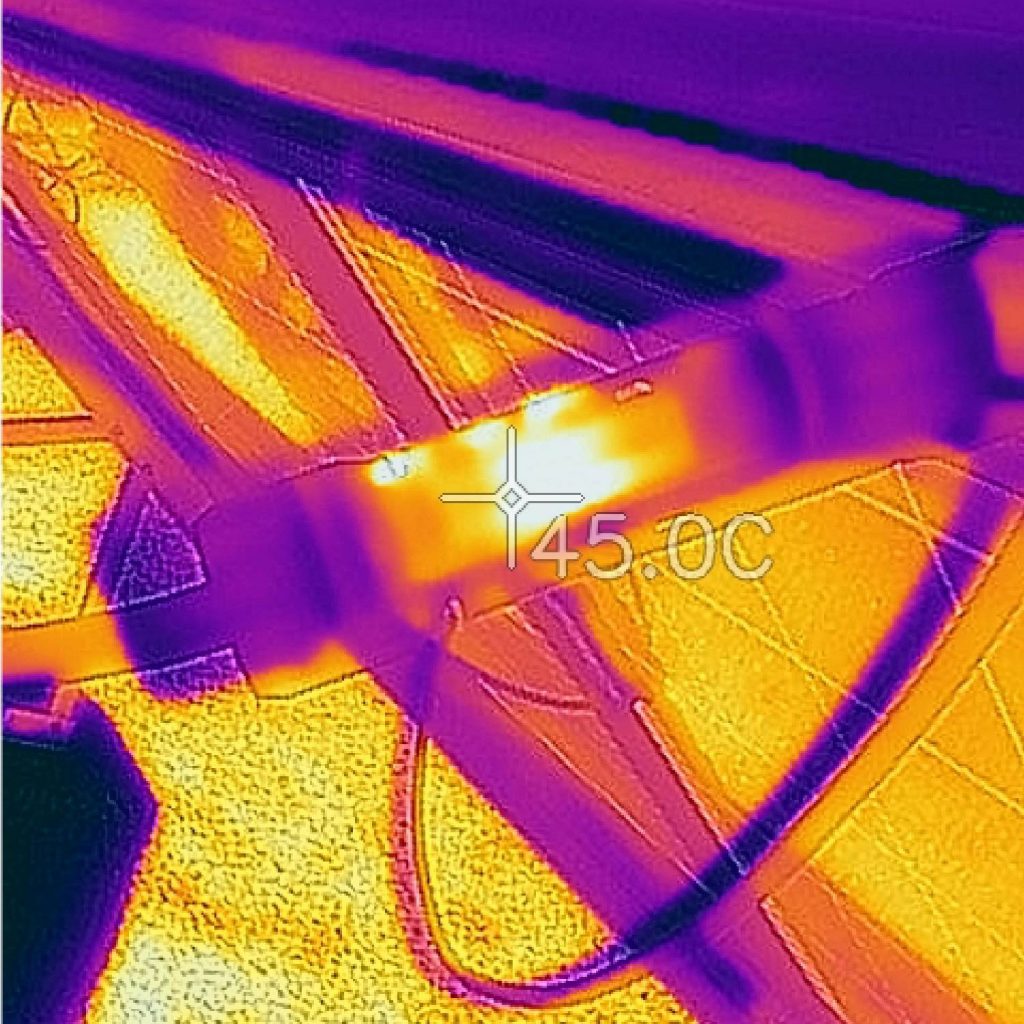
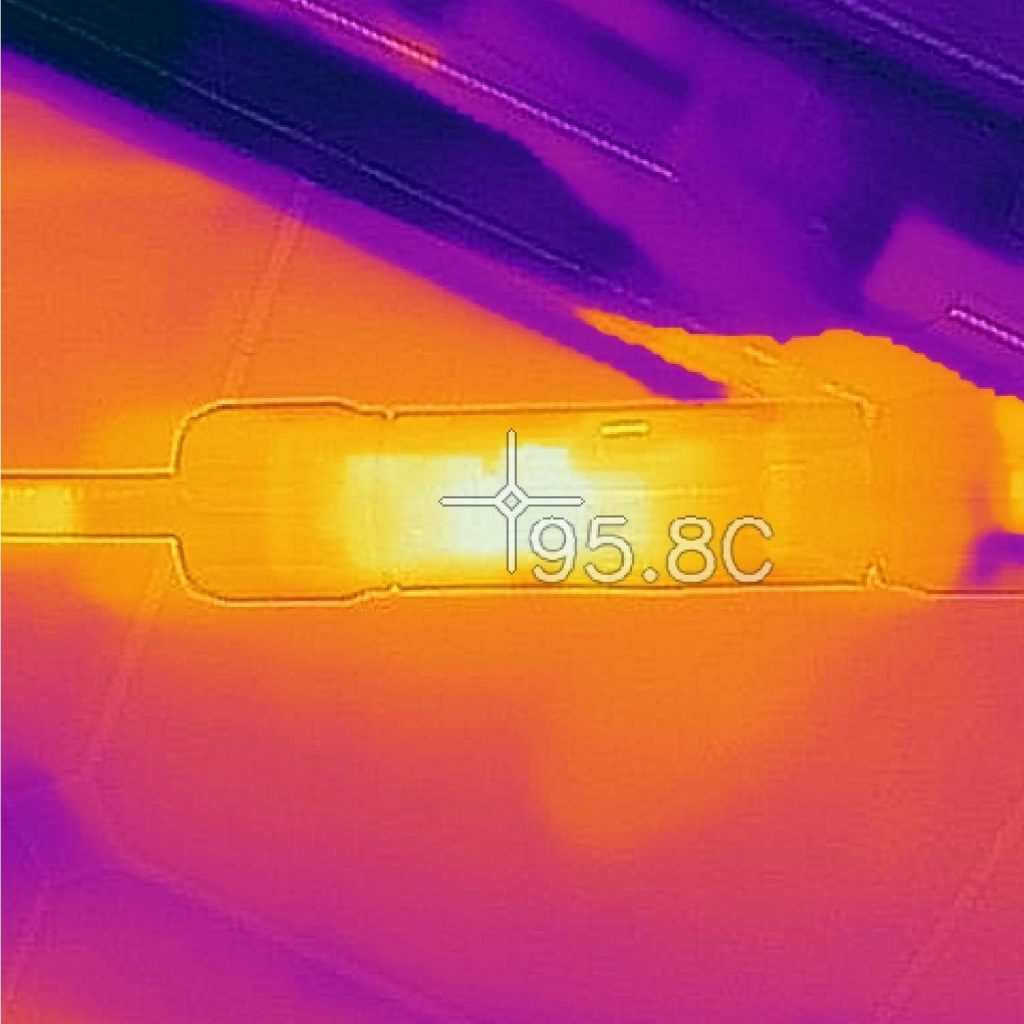
Thermal images such as the infrared images shown here are a good diagnostic tool for PV connectors. A sampling of fielded connectors reveals a range in operating temperatures from normal (25 to 27 °C) to very hot (95°C), indicative of high resistance and a significant safety risk.
Why This Work Matters
Connectors have historically been viewed as essential—but relatively uninteresting—components of a PV system, with a functional role that has been overshadowed by the industry’s focus on module efficiency and lower manufacturing and installation costs. Yet defective and degraded connectors affect system performance in profound ways, from power losses to increased O&M needs, to catastrophic failure and fire. In addition,degrading and failed connectors raise the specter of higher insurance rates, levelized cost-of-energy (LCOE) increases, and decreased confidence in the reliability of solar-generated power.
Overall, the data generated from this project will help drive the industry toward higher-quality connectors and improved installation practices, thus increasing the performance, reliability, safety and availability of the US solar infrastructure.
Why Now
Preliminary evidence suggests that connector failure is a rising threat to PV system reliability and to a PV plant’s operating costs, with failures driven by multiple factors:
- Lack of compatibility standards prior to 2020 for connectors from different manufacturers;
- Inadequacies in today’s codes (e.g., lack of materials standards);
- Installation practices that leave connectors open to soiling and moisture ingress before the system is fully wired;
- Weak bill-of-materials requirements, making it impossible to know the metallic alloys in the connector, despite the sensitivity of some metals to high humidity and other environmental stressors;
- Supply-chain pressures that lead to cost-cuts in manufacturing, including materials substitution and reduction;
- Prevalence of low-quality replacement connectors that are vulnerable to ingress of moisture /and particulates.
A Four-Part Investigation
Our research spans four topic areas:
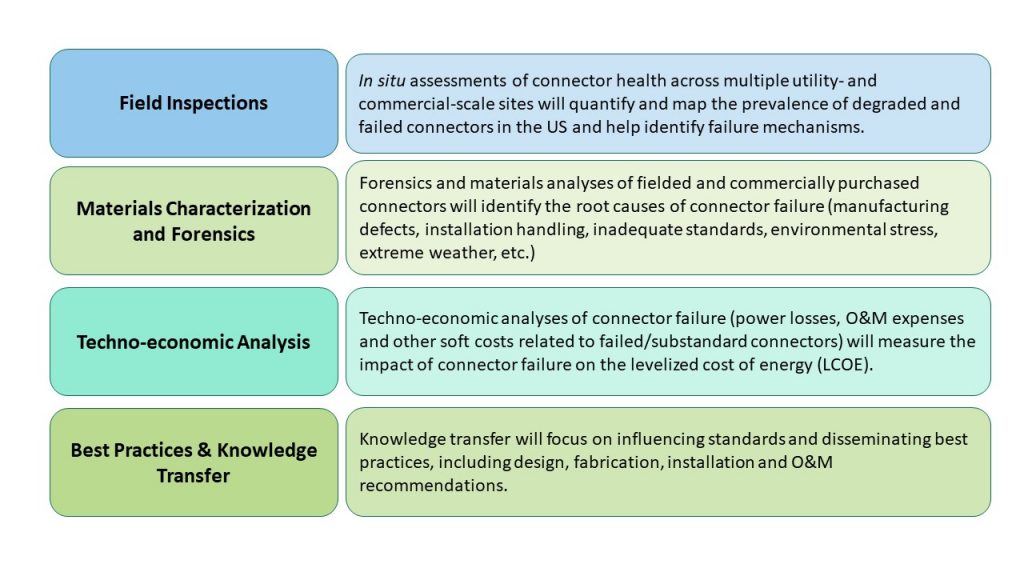
How Do Connectors Work?
PV connectors link a module’s electrical cables to those of adjacent modules, forming a string of modules that then feed their collective solar-generated electricity to the grid. Made with male and female ends, the metallic pin and corresponding socket should fit tightly together to prevent moisture and particulate ingress and friction, all of which can lead to corrosion and increased resistance, measured in ohms and manifested as power loss.
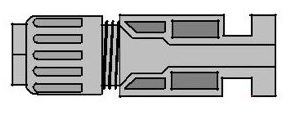
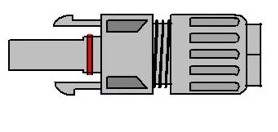
Male and female ends typically interlock to form a tight seal if they have the same morphology; connectors that are not identical in form can be forcefully inter-connected but put the integrity of the connector at risk. Also important to connector reliability is making sure the compression nuts at each end are properly tightened.
Areas of Research Focus
Field Inspections
Onsite inspections include 1) visual inspections for evidence of cross-mating, separation or loose connections, and signs of heat deformation; and 2) thermal inspection via a handheld long-wave infrared camera. Onsite data collection will include connector type, manufacturer and serial number (if known), location of connector in the array, and site metadata, including module make and model, system age, climate zone, exposure to extreme weather, etc. This task will also include development of a master spreadsheet to ensure thorough and consistent data across multiple sites.
Forensic Analysis
Connectors removed from PV systems as a result of onsite inspections, commercially off-the-shelf (COTS) connectors and connectors obtained via the project’s mail-in program, will be subjected to materials characterization and forensics analysis. The COTS connectors will represent a statistically significant number of each type, based on such data as market share, unit price, morphology and country of origin, and will provide important data on the variation in quality of connectors being sold in the US.
Overall, this lab-based work has four parts:
Techno-Economic Analysis
Techno-economic analysis (TEA) data will be collected in parallel with field data and industry interviews to quantify the impact of connector failure on PV lifecycle economic metrics, including energy yield, O&M expenses and levelized-cost-of-energy (LCOE). This work will include the modeling and analysis of power losses, O&M expenses and other soft costs related to failed connectors and will measure the impact of connector degradation and failure on a plant’s LCOE.
Knowledge Transfer and Dissemination of Best Practices
The results of this investigation will be publicly released, although the data will be aggregated and anonymized, in compliance with confidentiality agreements, to:
- Raise awareness regarding specific vulnerabilities
- Share risk-reduction strategies and best practices based on field and laboratory data
- Encourage information sharing across the solar industry
The results of this investigation will be publicly released, although the data will be aggregated and anonymized, in compliance with confidentiality agreements, to:
- Raise awareness regarding specific vulnerabilities
- Share risk-reduction strategies and best practices based on field and laboratory data
- Encourage information sharing across the solar industry
This work is funded in part or whole by the U.S. Department of Energy’s Solar Energy Technologies Office.
Related Research at NREL – Balance of Systems (BOS) Project
The National Renewable Energy Laboratory (NREL) has received funding from the U.S. Department of Energy for a related study, which is a durability assessment of the power transmission chain for utility-scale PV installations. It is broader in scope but is also exclusively laboratory-focused, including accelerated testing and associated forensics. Both teams are coordinating their efforts, with the intent of avoiding duplication of effort and creating efficiencies and sharing forensic methodologies.
Click to view BOS-related images below:
X-ray computed tomography (XCT): This image reveals the metal pins are not correctly connected within a field-failed cable connector, the consequences are revealed when the external plastic is removed. Image courtesy of NREL.
Comparing PV cable jackets: Comparing the surface roughness of un-aged and field degraded PV cable jackets. Image courtesy of NREL.
X-ray computed tomography reveals extent of damage: XCT reveals damage does not extend within a field-failed fuse block beyond the interconnecting lug. Image courtesy of NREL.
Prototype test fixture for Combined-Accelerated Stress Testing (C-AST): A prototype of a test fixture for Combined-Accelerated Stress Testing (C-AST). A pulley system is used to interface with the existing actuators (for mini-modules) to apply external mechanical deflection (where the magnitude of displacement may be adjusted in several locations). Image courtesy of NREL.
To join the “BOS Reliability” industry interface group or for more information about the project, contact: Dr. David Miller (NREL).
Principal Investigators:
- Dr. Laurie Burnham, Sandia, Principal Member of the Technical Staff
- Dr. Bruce King, Sandia, Distinguished Member of the Technical Staff
Other Technical Team Members:
- Wayne Li, EPRI
- Tapasvi Lolla, EPRI
- Vignesh Ramasamy, NREL
- Andy Walker, NREL
Partner with Us
To achieve our research objectives, we need asset owners and other stakeholders to give us access to their solar plants and participate in our mail-in program. In return for site privileges, Sandia will share data collected from those sites, including diagnostic and forensics findings, directly with the owners, or other persons of authority, along with any onsite observations that could improve plant reliability.
Note: All site data will be protected under a confidentiality agreement; the only data that is published, or otherwise shared externally, will be aggregated and anonymized and not traceable to a specific company or site.
Site Access
Sandia will conduct inspections of installed connectors across a variety of PV plants, representing a range of technologies, climates, geographies and years of operation. It is not our intent—nor is it within the scope of the project—to visit every site in the US; instead, we will select sites that are most representative of the majority of PV plants in the US. Site visits will include:visual and thermal inspections for evidence of cross-mating, separation or loose connections, heat deformation and operating temperatureinterviews with field crews regarding installation and O&M practicesdata collection, including connector make and model; serial number (if known); also site metadata, including module make & model, system age, exposure to extreme weather, etc.
Mail-In Program
To participate, or for more information, please contact Laurie Burnham, lburnha@sandia.gov
Dr. Laurie Burnham; lburnha@sandia.gov