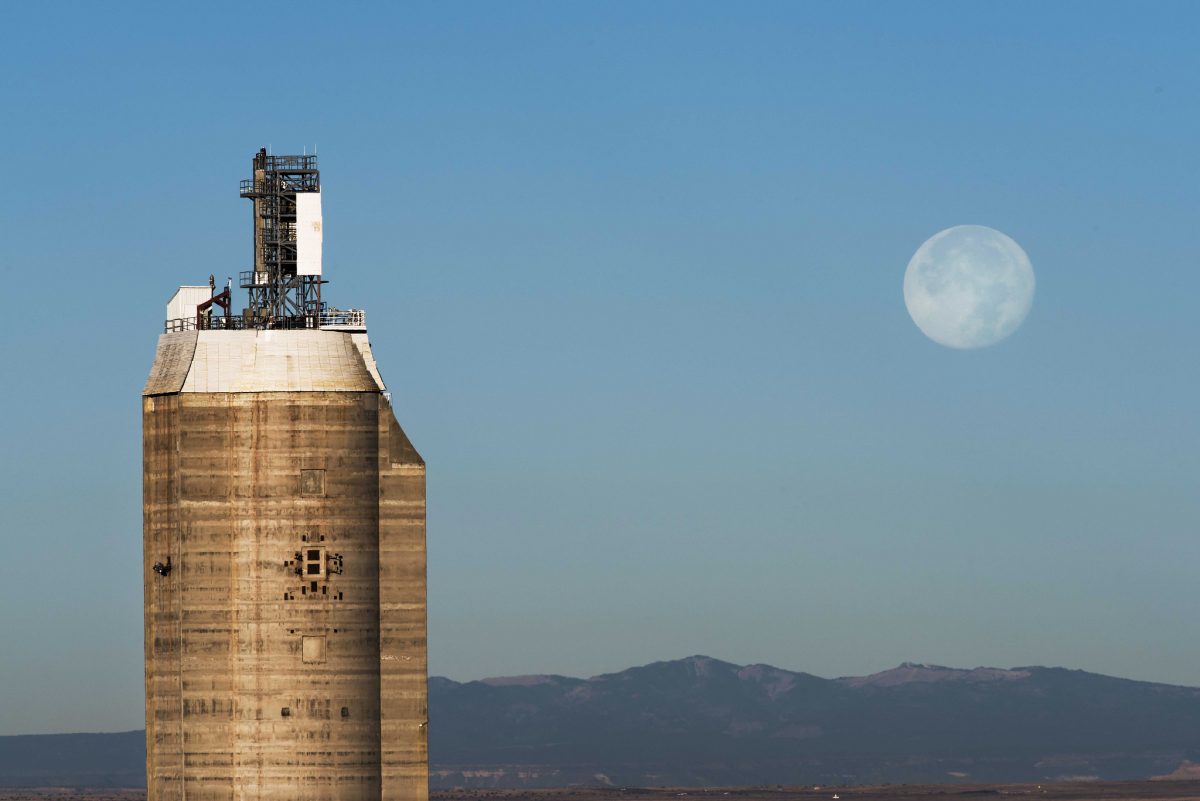
On this page:
Computational Modeling Research Capabilities | Molten Salt Research Capabilities | Chemistry Research Capabilities | CSP Design Capabilities | Optics Research Capabilities | Mechanical Fabrication Research Capabilities | Coatings Research Capabilities
Computational Modeling Research Capabilities
At the National Solar Thermal Test Facility (NSTTF), the CSP team has the research capabilities to perform high-flux, high-temperature testing for concentrating solar thermal applications including receivers, storage, heat exchangers, and conveyance to evaluate thermal-fluid processes of various heat-transfer media. The team also has access to numerous thermal-fluid laboratories across Sandia to test materials and processes, and validate models.
Molten Salt Research Capabilities
SNL and NREL are developing a 2.2-MWt liquid pathway (ternary chloride molten salt or sodium alkali metal) system consisting of a solar receiver, thermal energy storage tanks, and associated pumps, heat exchangers, piping, valves, sensors, and heat tracing. Additionally, at the NSTTF, the CSP team has worked and researched the capabilities of the Molten-Salt power development for decades. On-site, the CSP team has designed a Molten Salt Test Loop (MSTL) to allow industrial customers and researchers to test molten salts over a range of temperatures within energy-generation individual components such as flex hoses, ball joints, and valves, up to full solar collecting and heated systems. The system has 3 parallel test loops, made from 345H stainless steel, that provide locations where a customer’s experiment can be attached for testing in flowing salt in plant-like conditions. The system can accept and remove up to 1.4 MWth input from the system by either pump work or by heat input from the experiment. Anticipated experiments include flowing salt corrosion tests and accelerated life testing of components for both CSP and other molten salt applications, which could include nuclear energy, among other industrial thermal storage systems. Flanges that have been employed are Grayloc brand 6” hubs with silver coated seal rings. More comprehensive inspections of the MSTL show that it requires maintenance to become operational again, including re-melting the existing solar salt inventory.
Also, the CSP team has Molten Salt Test Pots that are capable of heating salts to 600°C or more depending on the set of conditions. Tanks are currently made from 321 Stainless Steel with internal heating rods to heat the salts. The tanks are well insulated and can be used for continuous operations.
Molten Salt Dynamic Testing System
Thermal performance, cycling and accelerated-life tests were conducted with NSTTF thermocline test facility capabilities, where samples were held in a vessel and molten salt was passed through the samples from two tanks. The tests showed that quartzite and silica sand best held up to the cycling with nitrate salt, which from the investigation were the most economical, and are more readily available than other materials tested. The system was constructed using welded 316 stainless steel piping and components. A small 10.2 cm diameter test chamber 35.56 cm tall containing filler material was placed between two vessels—the hot and cold tanks—each 25.4 cm diameter by about 152 cm tall. The hot tank was designed to contain molten salt at 450°C and the cold tank at about 285°C. Two gate valves and a drain valve were installed for periodic isolation and draining for sample observations. The system was carefully heat traced, thermocouples were installed, and the system was insulated to minimize heat loss while still allowing thermal cycling to occur. The filler medium test chamber and components were carefully fabricated to ensure containment of the mineral/sand samples while still allowing molten salt flow in either direction during thermal cycling. Research has been performed to develop a future system, with higher-temperature alloys, ceramics and/or coatings for higher-temperature molten salts testing, such as with chlorides, carbonates and fluorides.
SNL Molten Salt Chemistry Capabilities
The NSTTF extended research group, in connection with the Sandia-Livermore site, has conducted a great deal of work in the areas of molten salt corrosion and materials characterization degradation analysis. Static immersion tests previously conducted by SNL staff at the NSTTF tested coupon samples which were immersed in binary nitrate salts at temperatures of 400, 500, 600, and 680°C, with air sparging on all tests. Test samples were mounted on sample trees and separated by ceramic beads, then immersed in the binary solar salt at a given temperature. Air was sparged through a cross drilled tube to provide mixing of the salt and ensure that the partial pressure of O2 was consistent throughout the course of the experiments, for the sake of salt chemistry through the nitrate/nitrite equilibrium. Samples are nominally removed at intervals of 500, 1000, 2000, 3000, and 4000 hours to acquire data on time varying weight gain information while simultaneously employing metallography to identify corrosion mechanisms occurring within the melt. The purpose of these tests is to provide initial data on relative performance between these alloys and to determine changes in corrosion mechanisms as a function of temperature. The molten salt chemistry laboratories at SNL are also capable of obtaining thermophysical data pertaining to salt composition after thermal cycling and other thermal stress tests. Microscopy capabilities at SNL can also be employed to determine relevant corrosion reactions that occur during molten salt exposures to various stainless steels and Ni-based alloys. Scanning electron microscopes (JEOL JSM 840A) equipped with energy dispersive spectroscopic systems (Thermo Electron Corp) have previously been used where generated images are used to correlate the presence of an element within a given area. Research has also been previously performed for analysis of other molten salts such as chlorides and carbonates, which can also be extended to fluoride salts. Chloride and fluoride salts are susceptible to high corrosion rates in the presence of moisture and oxygen. Purification techniques have previously been conducted and are extremely important to ensure good materials performance, as formation of protective layers does not readily occur. Research for these types of purification techniques can be extended from chloride to fluoride salts in addition to compatibility research for cover gases used within fluoride molten salt reactors. Materials performance and reliability expertise and capabilities at SNL include static, tilted table, natural convection, and forced convection corrosion tests, which have been performed using a variety of SS and Ni-based alloys and ceramics, which can be extended for fluoride salts.
Molten Salt Test Pots
- The salt pot tanks are material testing tanks that are capable of heating salts to 600°C or more depending on the set conditions. This temperature limit is primarily due to salt decomposition of the nitrate salts, as well as salt pot containment material constraints.
- Tanks are currently made from 321 Stainless Steel with internal heating rods to heat the salts. The tanks are well insulated and can be used for continuous operations. However, proposals have been developed for adding SiC, higher-temperature alloys and refractory material liners to test chloride and carbonate molten salts.
- SNL has used a number of these pots for internal DOE studies for molten salts. A molten salt company, specializing in producing industrial grade salts, SQM, has also used this experimental setup to evaluate the effects of heating on different salt types and materials that can be used with those salts.
- This experimental setup is low-cost, with most of the cost being occurring at startup. The “trees” are often custom fit for the type of material sampling required. The material samples can be removed periodically to determine corrosion or other heating effects.
- A typical test including startup could range from $20k-$100k depending on the test setup and duration of testing with required intervals to check on the material samples.
- Previous research with these salt pots have included isothermal tests to evaluate the long-term durability of various alloy and thermocline materials, such as Stainless steels, as well as quartzite rock and silica sand respectively, that were statically immersed in ternary nitrate molten salts at both 450°C and 500°C.
- Research has been performed to add a composite SiC liner for higher-temperature molten salts testing, such as with chlorides, carbonates and fluorides.
Point of Contact: Kenneth Armijo
Chemistry Research Capabilities
At the National Solar Thermal Test Facility, the CSP team has the chemistry research capabilities to perform Reduction/Oxidation of Metal Oxides for Thermochemical Energy Storages, since current molten salt technologies are insufficient to store heat at temperatures passing the 1000°C. The CSP team has the capability to perform chemical research to bring the cost down, which demands high energy solutions.
CSP Design Capabilities
The NSTTF was founded in 1978 and began testing with high heat flux during that same year. The site has and is currently supporting all aspects of CSP including: optics (heliostats, dishes, metrology), high temperature receivers, balance of plant systems, heat transfer fluids/media, and heat flux measurement. Experts at the facility are currently working on projects to develop and commercialize falling particle receivers, high temperature salt systems, aerial drone utilization for metrology and alignment, and heliostat designs. The current test facilities include a solar tower and heliostat field with maximum heat flux input of 250 W/cm2, a solar furnace with a maximum heat flux input of 600 W/cm2, a solar simulator with a maximum heat flux input of 120 W/cm2, an optical metrology laboratory, and high temperature ovens. The CSP team has studied and designed components and materials to withstand the intense heating conditions, and is a world leader in CSP research. The facility is funded by the Department of Energy and supports customers with projects awarded from the DOE, as well as industrial partners and other government entities.
Point of Contact: Margaret Gordon
Optics Research Capabilities
The National Solar Thermal Test Facility (NSTTF) has an extensive research capability in the field of optical analysis and development. The NSTTF has optical facilities and tools that help researchers achieve optical studies in the area of Concentrating Solar Power (CSP). The CSP team has the Optics Lab, which is a local laboratory at the NSTTF site. The lab is capable of studying optical characterization of heliostat and dish facets. With the help of optical tools like AIMFAST and SOFAST, the CSP team can study and develop optical methods for heliostat designs. The tools are also applicable to assembly/production line environments. In addition, field support for characterization and alignment of CSP systems is provided. SOFAST, a highly accurate fringe-reflection-based measurement tool, is used to characterize and set the focus heliostat facets in the laboratory. HFACET is an optical-based alignment tool that is used to efficiently re-align the facets after re-attaching them to the heliostat. AIMFAST is used to characterize dish facets and align dish systems. Reflectance (q) is a measurement set-up to measure the surface solar-weighted reflectance versus angle of incidence.
Point of Contact: Randolph Brost
Mechanical Fabrication Research Capabilities
At the National Solar Thermal Test Facility (NSTTF), the CSP team has experienced mechanical technologists capable of designing and building mechanical components for CSP technologies. The NSTTF has a large machine shop equipped to maximum capacity for mechanical fabrication. It contains saws capable of cutting materials 20 ft. in length at low tolerances, and a magnetic drill press. The mechanical technologists have the capabilities of welding using MIG, TIG, or Orbital methods, and have experience welding Haynes 230 and Inconel alloys. NSTTF also has the capacity to design and develop large test structures up to 20 ft. x 20 ft. x 20 ft. in dimension. The following list includes mechanical fabrication that NSTTF Mechanical technologists can facilitate.
Machinery:
- Lathe capable of turning down pipes (3” capacity)
- Shear (8’ x 4’ x 0.25” capacity)
- Mills for fine tuning cuts
- Solar engine repair
- High pressure system fabrication and installation
- 60 ft. manlifts for installation/repair
- 12,000 lb. rough terrain telehandler forklift
- 8,000 lb. slab forklift
- 10,000 lb. rough terrain telehandler forklift
- Large platform scissor lift (30’ reach)
- Jib Cranes x 2 (10,000 lb. each) in the tower for fabrication at base of tower
- Bridge crane in high bay fabrication area (10,000 lb.)
Point of Contact: Margaret Gordon
Coatings Research Capabilities
To meet the SunShot goal of levelized cost of energy (LCOE) £ 6¢/kWh by 2020, next generation power towers will operate at temperatures > 600°C in order to take advantage of increased efficiencies of high-temperature operation. Current receiver coatings, such as Pyromark 2500, while highly absorbent, suffer from high emittance and have been reported to degrade during operation at T > 600°C. Here at the National Solar Thermal Test Facility, the CSP team is working to increase the thermal efficiency of SSA coating by 4% at 650°C, and 7% at 800°C, which can potentially reduce the LCOE by an estimated 0.25 ¢/kWh. Using the National Solar Thermal Test Facility facilities, the CSP team has the research capabilities to develop coating to effectively reach LCOE £ 6¢/kWh.
Other capabilities include:
- Optimizing spinel and thermal spray formulations
- Developing surface modification techniques to enhance solar selectivity
- Performance optimization of coatings supported by isothermal testing at temperature
- Refining coatings based on optical performance and durability.
Point of Contact: Andrea Ambrosini