Leading edge erosion is an emerging issue in wind turbine blade reliability, causing performance decreases and additional maintenance costs. Accounting for performance losses due to common blade surface roughness, such as dirt and insects, does not account for the increased performance loss due to the more severe surface roughness caused by the erosion of leading edge blade material. Results of an in-depth study indicated that a heavily eroded wind turbine blade can reduce annual energy production by up to 5% for a utility scale wind turbine.
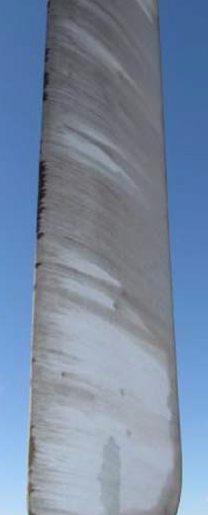
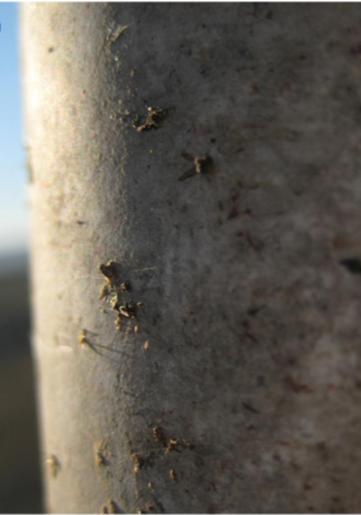
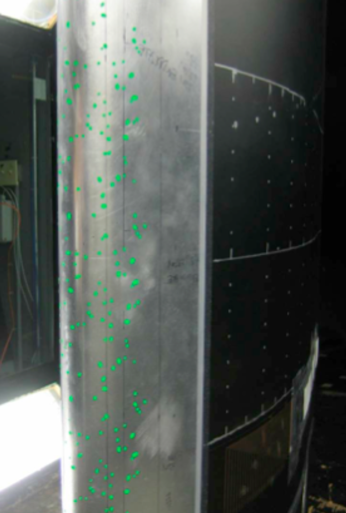
Example of a blade with severe leading edge erosion (left), a blade leading edge with observed field roughness (middle), and a wind tunnel model with distributed roughness elements (right)
Through the U.S. DOE Blade Reliability Collaborative, researchers from Sandia National Laboratories (SNL), Texas A&M, and U.C. Davis have recently addressed the subject of performance loss. This project includes roughness measurements at wind plants experiencing blade soiling and erosion, wind tunnel testing of airfoils with representative roughness and erosion levels, and the development of a computational model that captures the performance effects of blade surface roughness and erosion.
The surface roughness caused by blade leading edge erosion was characterized in the field and used with computational analysis to inform wind tunnel tests [1-4]. Researchers then used the wind tunnel measurements to develop a predictive model of roughness-induced boundary layer transition for wind energy applications [5-7]. A further analysis calculated the effects of erosion on wind turbine energy capture [8].
This first phase of measurement and modeling focused on an airfoil that is typically used on the tip region of a utility-scale wind turbine blade, the NACA 633-418, which has a maximum thickness to chord ratio of 18%. After this first phase of work, significant improvements were made to the computational roughness model [9, 10]. The aerodynamic characteristics of the thicker airfoils located at the inboard region of a wind turbine blade are significantly different than the characteristics of thinner, outboard airfoils. A second phase of this research focused on measuring the aerodynamic performance of an airfoil section model in a wind tunnel at conditions simulating those encountered by the inboard region of a wind turbine blade [11, 12]. The SERI S814 airfoil, which has a maximum thickness to chord ratio of 24%, was selected for this purpose due to it having desirable characteristics for code validation, as well as the availability of previously published transition data. The model was constructed using an innovative multi-part process, which will enhance the ability to locate transition using infrared thermography [12]. The computational roughness model was modified to be able to predict the performance of both of the tested airfoils using a multi-dimensional calibration technique [13].
The experimental results indicate that the effects of field roughness generally fall between clean airfoil performance and the effects of transition tape. Severe leading edge erosion can cause detrimental performance effects beyond standard roughness. The results also indicate that a heavily eroded wind turbine blade can reduce annual energy production by up to 5% for a utility scale wind turbine [8].
![Predicted AEP loss for NREL 5-MW turbine due to heavy leading edge roughness[6].](https://www.sandia.gov/app/uploads/sites/273/2017/07/aep-loss.png)
The wind tunnel data have been publicly released through the DOE Atmosphere to electrons (A2e) Data Archive and Portal.
The following papers have been produced through this work, and are available through the associated hyperlinks.
Publications
- Ehrmann, R.S., et al., Realistic Leading-Edge Roughness Effects on Airfoil Performance, in 31st AIAA Applied Aerodynamics Conference. 2013, American Institute of Aeronautics and Astronautics.
- Rumsey, M.A. Leading-Edge Erosion Measurements. in Blade Reliability Collaborative Meeting 2013. 2013. Albuquerque, NM.
- Wilcox, B. and E. White, Computational analysis of insect impingement patterns on wind turbine blades. Wind Energy, 2016. 19(3): p. 483-495.
- Ehrmann, R.S., et al., Effect of Surface Roughness on Wind Turbine Performance. 2017, Sandia National Laboratories: Albuquerque, NM. p. 114. SAND2017-10669.
- Langel, C.M., et al., A Computational Approach to Simulating the Effects of Realistic Surface Roughness on Boundary Layer Transition, in 52nd Aerospace Sciences Meeting. 2014, American Institute of Aeronautics and Astronautics.
- Ehrmann, R.S. and E.B. White, Influence of 2D Steps and Distributed Roughness on Transition on a NACA 63(3)-418, in 32nd ASME Wind Energy Symposium. 2014, American Institute of Aeronautics and Astronautics.
- Langel, C.M., et al., A Transport Equation Approach to Modeling the Influence of Surface Roughness on Boundary Layer Transition. 2017, Sandia National Laboratories: Albuquerque, NM. p. 100. SAND2017-10670.
- Langel, C.M., et al., Analysis of the Impact of Leading Edge Surface Degradation on Wind Turbine Performance, in 33rd Wind Energy Symposium. 2015, American Institute of Aeronautics and Astronautics.
- Langel, C.M., R. Chow, and C.P. VanDam, Further Developments to a Local Correlation Based Roughness Model for Boundary Layer Transition Prediction, in 53rd AIAA Aerospace Sciences Meeting. 2015, American Institute of Aeronautics and Astronautics.
- Langel, C.M., R. Chow, and C.P. VanDam, A Comparison of Transition Prediction Methodologies Applied to High Reynolds Number External Flows, in 54th AIAA Aerospace Sciences Meeting. 2016, American Institute of Aeronautics and Astronautics.
- Maniaci, D.C., et al., Experimental Measurement and CFD Model Development of Thick Wind Turbine Airfoils with Leading Edge Erosion. Journal of Physics: Conference Series, 2016. 753(2): p. 022013.
- Wilcox, B., E.B. White, and D.C. Maniaci, Roughness Sensitivity Comparisons of Wind Turbine Blade Sections. 2017, Sandia National Laboratories: Albuquerque, NM. p. 118. SAND2017-11288.
- Langel, C.M., et al., RANS Based Methodology for Predicting the Influence of Leading Edge Erosion on Airfoil Performance. 2017, Sandia National Laboratories: Albuquerque, NM. p. 172. SAND2017-11289. Edit