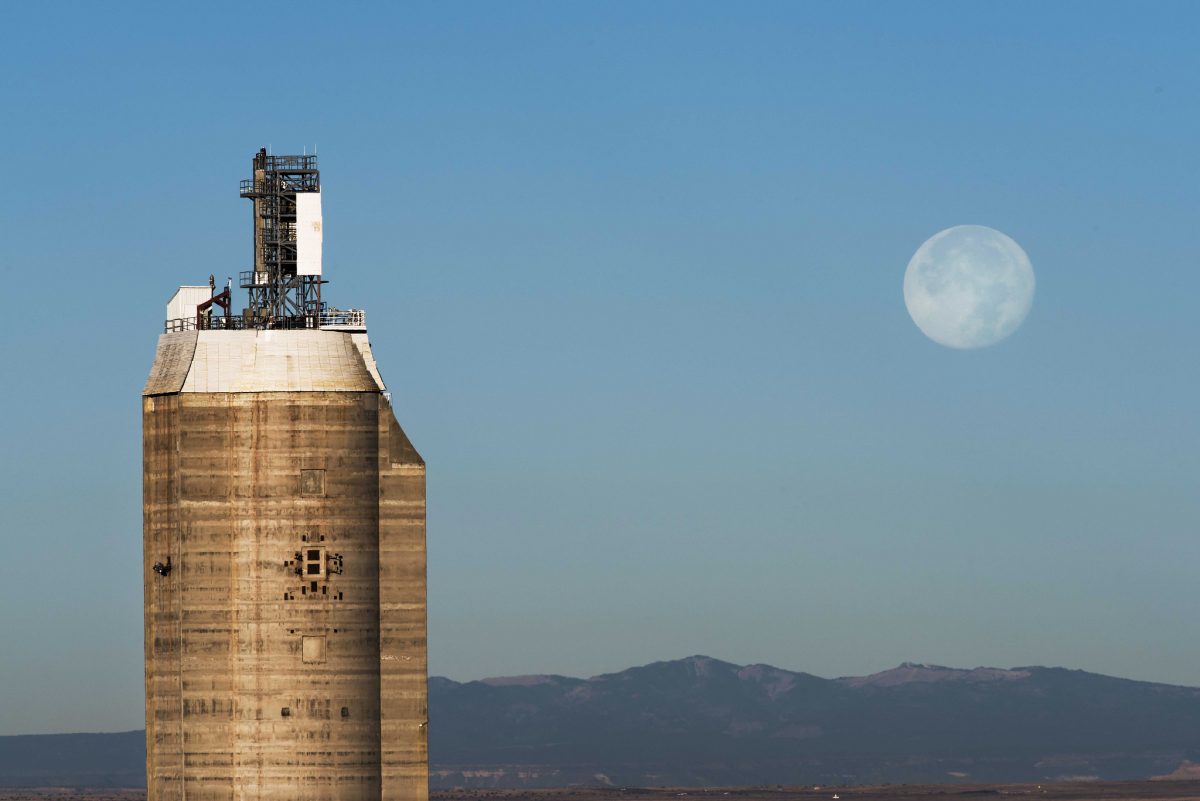
On this page
- Gen 3 Particle Pilot Plant (G3P3): Integrated High Temperature Particle System for CSP
- Gen 3 Liquid-Pathway to SunShot: Solar Tower Integrated Molten Salt/Sodium High-Temperature System for CSP
- sCO2 Loop in Support of the CSP Gen 3 Solid, Liquid, and Gas Pathways
- Characterization of Convective and Particle Losses in High-Temperature Particle Receivers
- High-Temperature Particle Heat Exchanger for sCO2 Power Cycles
- Advanced Supercritical Carbon Dioxide Cycles (APOLLO)
- Solar Thermal Ammonia Production (STAP)
- DC Arc-Flash Safety for 1,500VDC:Methodology, Verification and Codifying
- UFACET (SETO Lab)
- Electro-Dynamic Screens (EDS) for Water-Free Mirror Cleaning (APOLLO)
- Metamaterials Based Dielectric Concentrator (COLLECTS)
- Optical Tools Development
- Evaluation of Fluidic Diodes for Solar Collectors (NMSBA)
- Beamed Energy Project
Gen 3 Particle Pilot Plant (G3P3): Integrated High Temperature Particle System for CSP
The objectives of the Gen 3 Particle Pilot Plant (G3P3) project are to design, construct, and operate an integrated system that de-risks a next-generation, particle-based concentrating solar power (CSP) technology to produce clean, utility-scale electricity with long-duration energy storage. The proposed multi-MWt G3P3 system will utilize the existing field of heliostats at Sandia’s National Solar Thermal Test Facility (NSTTF) to concentrate the sunlight to a particle receiver that heats particles to over 700 °C, enables at least six hours of particle-based energy storage, and heats a working fluid (e.g., sCO2 or air) to ≥ 700°C while demonstrating the ability to meet cost and performance goals.
Particle receivers are being pursued to enable higher temperatures (>700°C) with direct storage for next-generation dispatchable concentrating solar power (CSP) plants, process heating, thermochemistry, and solar fuels production. Unlike conventional CSP receivers that use fluids flowing through tubes, the proposed particle-receiver system uses solid particles (ceramic or sand) that are heated directly as they fall through a beam of concentrated sunlight. Once heated, the particles are stored in an insulated bin before passing through a particle-to-working-fluid heat exchanger to power a high-efficiency Brayton cycle (e.g., sCO2 or air). The cooled particles are collected and then lifted back to the top of the receiver.
The success of this work will retire the primary risks associated with particle receivers and enable the successful demonstration of a high-temperature particle pilot plant that meets SunShot goals with thousands of hours of on-sun testing. Successful operation of G3P3 will lead to broader acceptance, deployment, and commercialization.
Learn more about G3P3
Point of Contact: Jeremy Sment
Gen 3 Liquid-Pathway to SunShot: Solar Tower Integrated Molten Salt/Sodium High-Temperature System for CSP
The objective of this research is to design, develop, test at small scale, and validate at 2-MWt, a liquid-phase system consisting of the solar receiver, thermal energy storage (TES) unit, primary heat exchanger, and associated pumps, piping, valves, sensors, and heat tracing. The tasks are divided into two locations and areas: 1) The USA-site work will focus on MgCl2-based salts with direct 2-tank storage; and 2) Complementary work in Australia will focus on a sodium receiver with heat exchange (HX) into salt-based storage. A single, integrated concept will be proposed for Phase 3 demonstration. The data generated from the 2-MW pilot testing will inform system models used to show how the demonstrated technology can be employed at 100-MWe scale to achieve the SunShot goal of 6 ¢/kWh electricity from CSP.
As receiver temperature advances from the current range of 570°C up to 720°C, achieving the targeted 90% optical/thermal efficiency will be important where new receiver coatings and geometries are required. SolarReserve, during their DOE-funded projects, analyzed the baseline design for chloride salt, a tubular receiver. The work concluded that a tubular design was feasible, where preliminary data and molecular theory suggest that the ternary salt will have slightly more favorable properties than the binary salts that have been previously explored. In addition, the team will explore enhancements to the salt and to piping system design and layout to improve heat-transfer rates. An additional mitigation approach explores a completely different fluid in the receiver. Work in Australia will investigate a sodium receiver. The properties of sodium suggest that 90%-efficient receivers can be designed with existing technology (Polimeni, et al., 2017). An alternative that uses salt storage with sodium as the heat-transfer fluid (HTF) is planned to leverage that fluid’s ability to support higher flux limits on the receiver.
Point of Contact: Kenneth Armijo
sCO2 Loop in Support of the CSP Gen 3 Solid, Liquid, and Gas Pathways
This project seeks to design, assemble, perform acceptance testing, and deploy a 1 MWth-scale supercritical carbon dioxide (sCO2) support loop to provide cooling to the primary heat exchanger of the Gen3CSP pilot plant. Although the components between the thermal storage system and primary heat exchanger differ with each Gen3CSP heat transfer media phase (solid, liquid, and gas), all three systems intend to transfer heat to an sCO2 Brayton cycle for improved power conversion efficiency over steam Rankine systems. The sCO2 support loop provides cooling to the pilot plant primary heat exchanger with the same conditions as a power conversion cycle in order to fully demonstrate all heat transport system components from sun to sCO2.
Sandia will leverage the lessons learned from over a decade of sCO2 system design and operational experience across the international research community in order to develop a capable, compact, and cost effect sCO2 support loop. System design requirements will be developed and monitored in coordination with the Gen3CSP pilot plant teams in order to ensure the impact of any design decisions are accounted for in all projects. A design study will be completed under Phase 1 of the work and reviewed by the Gen3CSP pilot plant teams to ensure all requirements have been met. The support loop will be procured and constructed under Phase 2 with shakedown testing to verify system capabilities. Finally, under Phase 3, the support loop will be integrated with the Gen3CSP pilot plant to demonstrate a complete thermal power system.
To learn more, visit the Gen3 CSP Lab Call project profile.
Characterization of Convective and Particle Losses in High-Temperature Particle Receivers
The objectives of this work are to develop tools and methods to characterize particle and heat losses emitted from the aperture of a high-temperature particle receiver, which can lower thermal efficiency, increase costs of particle replacement, and pose a particulate matter (PM) inhalation risk. Models will be developed to characterize and understand the particle fluid dynamics and heat transfer during these processes, and sensing/imaging methods will be developed and tested to characterize particle and heat losses. Laboratory experiments and on-sun testing will be performed to validate the models, methods, and tools. This work will also provide a quantitative determination of PM inhalation safety risks.
To learn more, visit Characterization of Convective and Particle Losses in High-Temperature Particle Receivers
Point of Contact: Jeremy Sment
High-Temperature Particle Heat Exchanger for sCO2 Power Cycles
This work will design, develop, and test a particle/sCO2 heat exchanger operating at temperatures ≥ 720°C and sCO2 pressures up to 20 MPa. Industry experience with similar heat exchangers is limited to lower pressures, lower temperatures, or alternative fluids such as steam or water. Concentrating Solar Power is partnering with heat exchanger manufacturers to develop and down-select several designs for the unit that achieves both high performance and low specific cost to retire risks associated with a solar thermal particle/sCO2 power system. A prototype unit will be manufactured and tested in a high temperature and pressure sCO2 flow loop to confirm key metrics for performance and cost. Lessons learned and experiences gained will be used to scale-up the design to a multi-megawatt plant with cost estimates and uncertainties.
Point of Contact: Jeremy Sment
Advanced Supercritical Carbon Dioxide Cycles (APOLLO)
Current steam Rankine cycles used for power conversion at CSP plants have thermal to electric efficiencies ranging from 30% to 35% and rely on massive shell and tube heat exchangers and steam turbines. sCO2 Brayton power cycles could provide thermal to electric conversion efficiencies above 50% and take advantage of compact heat exchanger and turbomachinery technology. These combined effects can significantly reduce the installation and operational costs of CSP plants with thermal storage allowing for cost-effective solar energy at any time of the day.
Researchers at the University of Wisconsin–Madison (UW), Colorado School of Mines, Sandia National Laboratories (SNL), and the National Renewable Energy Laboratory (NREL), in collaboration with the companies FlowServe and Comprex, will design, fabricate, and test a fixed bed regenerator system that is compatible with the operating conditions expected in a sCO2 cycle. Lab- and prototype-scale regenerator systems will be fabricated and installed at UW and SNL in order to validate design and operational expectations. These results, in combination with cycle modeling for scaled-up regenerator performance, will allow for the improvements in power block and overall plant levelized cost of electricity (LCOE) and internal rate of return (IRR) as compared with fully-recuperated cycles.
Point of Contact: Henk Laubscher
Solar Thermal Ammonia Production (STAP)
Ammonia (NH3) is an energy-dense chemical and a vital component of fertilizer. In addition, it is a carbon-neutral liquid fuel and a potential candidate for thermochemical energy storage for high-temperature concentrating solar power (CSP.) Currently, NH3 synthesis occurs via the Haber-Bosch process, which requires high pressures (15-25 MPa) and medium- to high- temperatures (400-500°C). N2 and H2 are essential feedstocks for this NH3 production process. H2 is generally derived from methane via steam reforming; N2 is sourced from air, after oxygen removal via combustion of hydrocarbons. Both processes consume hydrocarbons, resulting in the release of CO2. In addition, hydrocarbon fuels are burned to produce the heat and mechanical energy required to effect the NH3 reaction, further increasing CO2 emissions.
The development of a renewable pathway to NH3 synthesis, which utilizes concentrated solar irradiation as a process heat instead of fossil fuels and operates under low or ambient pressure will result in both a decrease (or elimination) of greenhouse gas emissions as well as avoid the cost, complexity, and safety issues inherent in high-pressure processes. We propose to develop a solar thermochemical looping technology to produce and shuttle N2 from air for the subsequent production of ammonia via an advanced two-stage process. Concentrated solar irradiation first drives an endothermic reduction of redox-active metal oxide particles; subsequent exposure to air re-oxides particles, removing the oxygen (O2) and producing nearly oxygen-free N2 gas, designed to whatever purity level is necessary for the next reaction step. This process cycles indefinitely and requires little to no conversion of thermal energy to electrical energy and no pressurization of air. The generated N2 can serve as a feedstock to a renewable NH3 production process, which can occur via an advanced two-step, low pressure, looping process. In the first step, reduced metal (or nitrogen deficient metal nitride) particles react with N2 to form a nitride. In the second step, H2 reacts with the resulting nitride to yield NH3. CSP’s concept will result in a cost-effective and energy-efficient technology for the renewable N2 production and synthesis of NH3 from H2 (produced from H2O) and air using solar-thermal energy from concentrating sunlight, under milder conditions than current NH3 production via the high-pressure Haber-Bosch cycle. Successful completion of this project will result in a demonstration of NH3 production via a renewable technology with a path forward to scale-up and integrate with a CSP plant.
Point of Contact: Andrea Ambrosini
DC Arc-Flash Safety for 1,500VDC:Methodology, Verification and Codifying
The emerging deployment trend towards 1,500VDC utility-scale PV plant architectures signifies the solar industry’s latest effort to reduce system costs. Higher voltages offer the potential to reduce upfront capital expense by $0.03-0.05/Wp, increase overall plant electrical efficiency, and perhaps reduce life cycle operating expenses. The first 1,500VDC plant was installed in Germany in 2012, and in the U.S. in 2014. A rapid shift towards higher plant voltages appears imminent based on the number of orders placed with equipment manufacturers offering 1,500VDC inverters and the number of plants currently in development and under contract. Figure 1 shows the predicted DC nameplate capacity of utility-scale PV plants that are expected to be globally installed each year utilizing the 1,500VDC architecture. It also illustrates the anticipated capacity as a percentage of all forecasted utility-scale projects, prognosticating over 90% market share adoption by 2020. [1], [2]
This project intends to increase the fundamental understanding of arc-flash hazards and codify the results, namely providing the quantitative foundation and recommendations for an IEEE code. This will be accomplished by physically testing arc-flashes in a laboratory; developing a detailed physics-based model to confirm underlying methodology and key input variables; as well as documenting and disseminating results through guidelines submitted to code bodies, journal and conference publications, and an easy-to-use incident energy calculator. The work to date has developed a fundamental framework for modelling an open-arc arc discharge between two electrodes. This model would include fundamental physics related to plasma physics and thermodynamics to determine incident energy and the zone of influence, which could later be scaled to photovoltaic (PV) balance of systems (BOS) applications. Sandia National Laboratories (SNL) has unique capabilities for investigating arc-fault phenomena in high voltage photovoltaic (PV) systems, with robust codes and standards progress in the field. Additionally, the SNL team has developed an experimental test bed (Figure 2), with a suite of plasma and thermodynamic characterization capabilities (Figure 3) that will feed the development of an in-house physics code, ARIA, to characterize open-air arc discharges, and later arc discharges from PV equipment. To date, some model-validation work has taken place, which can only be considered idealistic and one dimensional.
[1]1,500-Volt PV Systems and Components 2016-2020: Costs, Vendors, and Forecasts. GTM Research. January 2016.
[2]Global Solar Demand Monitor Q4 2016. GTM Research. November 2016.
Point of Contact: Kenneth Armijo
UFACET (SETO Lab)
This unmanned aerial system (UAS) based technology is used for optical assessments of heliostat collector field. In current development activities, the system assesses heliostat canting quality, and provides feedback for correcting the canting errors to better than 0.5 mrad.
Point of Contact: Randolph Brost
Electro-Dynamic Screens (EDS) for Water-Free Mirror Cleaning (APOLLO)
Sandia is supporting Boston University in their development of EDS technology for water-free mirror cleaning. This is achieved by embedding thin wire electrodes under the glass cover and using electro-statics to repel and remove dust off the mirror surface. Sandia is performing parametric optical studies on electrode geometries and layouts to maximize optical efficiency. The designs are modeled in optical codes for performance evaluations. The results of the optical performance evaluations are combined with the EDS performance to optimize the electrode geometry designs. The developed prototypes are evaluated at Sandia for performance and environment survivability.
Point of Contact: Randolph Brost
Metamaterials Based Dielectric Concentrator (COLLECTS)
Sandia supports University of California-San Diego’s development of metamaterials-based reflectors and concentrators. Unlike curved mirrors, metasurfaces can be nominally flat, and by creating the right surface micro- and nano-structures, the incident light can be manipulated to achieve various functions such as high reflections and concentrations. Sandia is providing consultations on metasurface fabrication processes. In addition, Sandia is evaluating prototype samples for environmental survivability.
Point of Contact: Randolph Brost
Optical Tools Development
Sandia is developing optical metrology tools for industry use for evaluation, validation and commissioning. Current tools under development include video-based PHLUX method (VPHLUX) and AIMFAST. VPHPUX will monitor flux on the receiver and provide flux variations on the receiver in real-time. AIMFAST is based on deflectometry (or fringe reflection technique) to assess heliostat or dish facet canting qualities and provide feedback for making corrections to facet alignments.
Point of Contact: Randolph Brost
Evaluation of Fluidic Diodes for Solar Collectors (NMSBA)
Sandia currently supports a local company to evaluate different fluidic diode designs through modeling and experimentation. The fluidic diodes will be incorporated into flat-plate solar collectors to provide passive cooling (i.e., temperature regulation) to the solar collector.
Point of Contact: Randolph Brost
Beamed Energy Project
Sandia National Laboratories is currently working with the Air Force Research Laboratory (AFRL) to leverage CSP Dish Stirling Engine technology for use in a terrestrial application to receive beamed millimeter-wave power and convert it to electrical power. To accomplish this, a Solar SOLO 161 Stirling engine power conversion unit (PCU) off-grid system is employed (Figure 1), with hydrogen used as the working fluid, and operated at temperatures and pressures as high as 775°C and 2,500 psi. The system is capable of generating up to 10 kW of electrical power. Follow-up research will investigate various receiver geometries, materials, and operational modes. The work is funded by the Operational Energy Capability Improvement Fund (OECIF), by the Air Force Office of Scientific Research under FA9550-17RDCOR449, and by the Air Force Research Laboratory. (AFMC-2019-0206)
Point of Contact: Kenneth Armijo