Reliability, Operations & Maintenance, and Standards
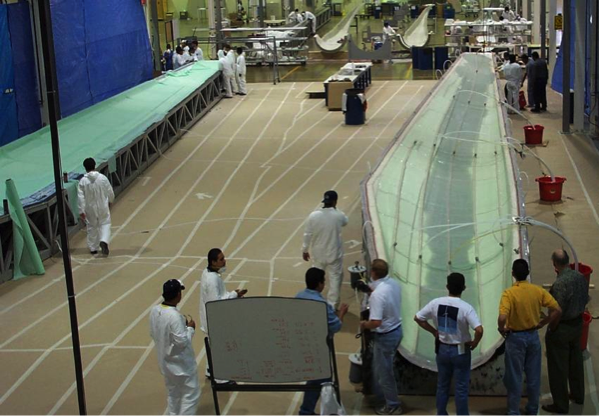
Blade reliability is one of the most costly elements of plant installation and operation because blade failure can cause extensive down time and lead to expensive repairs. The manufacturing process can be a significant source of defects due to the complicacy of producing very large composite structures with inexpensive materials and processes. Blades can also be damaged during the transportation and installation process. Finally, wind turbines operate in harsh environments where wind-blown particulates cause surface erosion and lightning strikes can sometimes destroy blades. The summary effect of these issues is that blades have been responsible for 11% of turbine downtime in recent years, which is the third largest source of any component. Furthermore, the amount of downtime attributed to blade failure has increased over the past few years, and it is anticipated that as rotors continue to grow to larger sizes, blade reliability issues could become more prominent.
The Sandia-led Blade Reliability Collaborative (BRC), funded by the U.S. Department of Energy, seeks to understand the root causes of premature blade failure and unplanned maintenance, and the most cost-effective methods to insure that blades can survive their expected operational life.
The current research work under the BRC focuses on examining flaws and defects resulting from the manufacturing process, as well as damage incurred during operation. Major area of focus include:
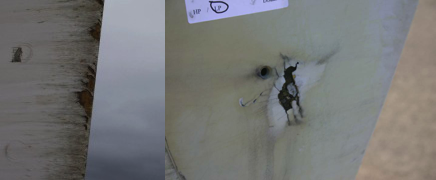
- the evaluation of nondestructive inspection (NDI) techniques and equipment in both manufacturing floor and field settings to assess their viability in terms of both accuracy and practicality;
- understanding the effects of leading edge erosion by the collection of field measurements of erosion profiles and performance degradation, the development of aerodynamic models through wind tunnel testing, and computational fluid dynamics (CFD) modeling; and
- development of high-performance computing (HPC) models to analyze the loads experienced during operation and the effects that these loads have on the initiation and growth of damage in flawed blades.
The Sandia project team has recently:
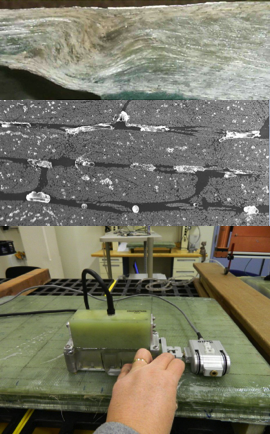
- designed and manufactured two small-scale validation blades containing highly characterized flaws;
- made detailed surface scans of utility-scale wind blades with eroded leading edges;
- conducted detailed investigation of manufacturer process to determine width of adhesive bond line at shear web to spar cap flange interface;
- tested a new, in-house designed pierced-bladder, phased-array probe holder that can be used with wide-area scanning techniques;
- performed wind tunnel testing of airfoils with leading-edge erosion; and
- developed new analysis methods to model wind blade leading-edge erosion.
Our future project goals are to:
- improve operational wind plant reliability by collecting data on blade defects and damage to guide research,
- advance blade standards by quantify uncertainty in analysis tools,
- inform reliability and performance testing through blade testing and model validation, and
- increase operational wind plant reliability by addressing operational damage caused by leading-edge erosion and lightning.