Rotor Innovation & Operations
Advanced rotor concepts—from aerodynamics, instrumentation and reliability —offer great potential for further improving wind plant performance and reducing energy costs. Sandia leads next-generation rotor development through:
- Open-source blade design platforms
- Custom tools for structural, aerodynamic, and cost design and analysis
- Sensors packages for structural & aerodynamic field testing
- Active and passive load alleviation technologies
- Evaluation of novel carbon fiber materials
- Durability and damage tolerant design
- Performance impacts from leading edge erosion
- Defect and damage analysis
The National Rotor Testbed
Sandia plays a key role in an unprecedented collaboration between the DOE’s Wind Program, the Advanced Manufacturing Office, multiple national laboratories and industry partners. The National Rotor Testbed (NRT) is a research-scale blade designed to replicate the wake of utility-scale rotors on a smaller, more cost-effective scale. It uses a suite of mechanical and aerodynamic sensors that enable model validation and data gathering. The NRT, which was manufactured from a first-ever 3D-printed mold, will be used for experimental campaigns at Sandia’s Scaled Wind Farm Technology Facility (SWiFT).
Read the design documentation for our new wind turbine blade design.
Rotor Simulation & Modeling
Sandia develops open–source rotor tools for rotor design and optimization. Our tools simplify the design process, allowing researchers to evaluate new, innovative concepts.
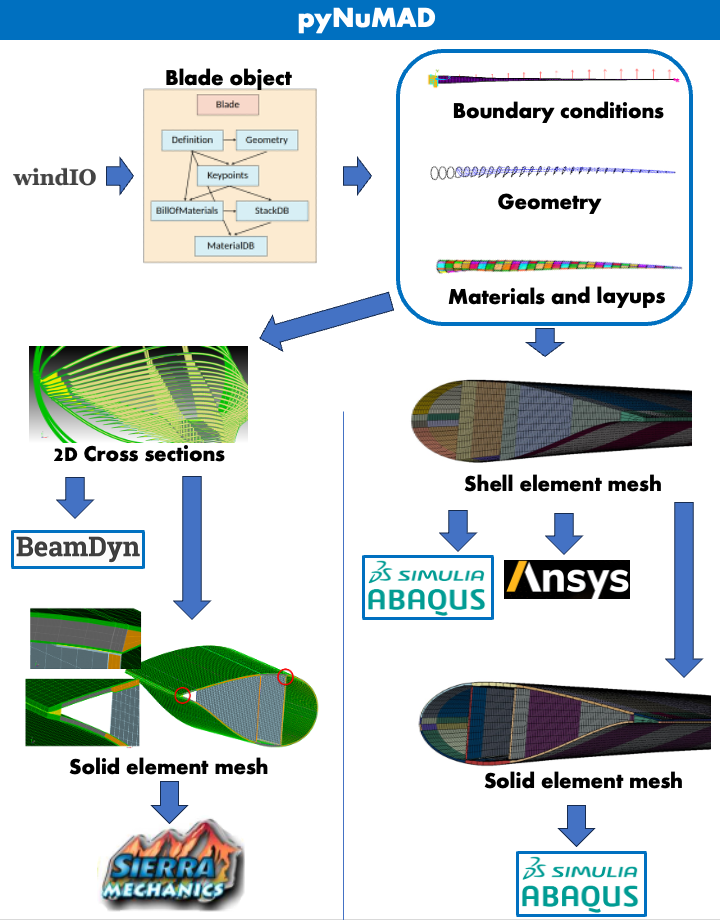
Blade Design
Python-Numerical Manufacturing And Design Tool or pyNuMAD is an object-oriented, open-source software program written in Python which simplifies the process of creating a three-dimensional model of a wind turbine blade. The tool organizes all blade information including aerodynamic and material properties as well as material placement into an intuitive API for use with other software.
Download pyNuMAD
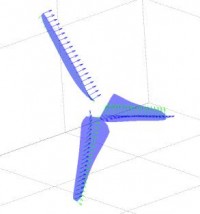
Turbine Simulation
CACTUS (Code for Axial and Cross-flow Turbine Simulation) is an open-source design and analysis package that uses the free wake vortex method to enable efficient simulation of turbine performance under operational and extreme conditions. Simulations only take minutes, which allows users to easily model multiple design iterations.
Download CACTUS
Sensors & Control Systems
Sandia has developed and fielded various sensors to directly or indirectly measure wind-load forces and structural dynamic response of the rotor in the field during operation in real-time. Measurements of rotor-blade strain, acceleration, and surface pressure via sensors mounted in the rotor are used to verify designs and discover new physics.
New sensors are readily integrated into the SWiFT site data and acquisition control system, which is time synchronized across the site.
Active & Passive Load Alleviation
A wind turbine’s sensors and control system is typically in the nacelle. However, mounting them on the rotor itself provides new information about dynamic loading and the ability to reduce loads through the use of advanced aero-structural feedback control. Sandia leads efforts to design, build and tests rotors with integrated sensor and control systems.
Click to view the SMART Rotor.
An example of Sandia’s work includes the design and demonstration of the SMART (Structural and Mechanical Adaptive Rotor Technology) rotor, a rotor with integrated control and sensor systems. In addition to demonstrating the value of active rotor control, this effort provided insight about predictive numerical models for active load control and future research areas.
Read the SMART Wind Turbine Rotor: Design Field Test report
Read the data analysis and conclusions of the SMART Wind Turbine Rotor project
Blade Optimization Studies
To reduce the cost of wind energy, Sandia optimizes and tests rotor designs. In 2014, Sandia partnered with the National Renewable Energy Laboratory (NREL) to study the effects of high tip velocities on the cost of wind energy. As part of this effort, researchers compared and optimized blade geometries to develop rotor aerodynamic designs that:
- were as light as possible,
- captured as much energy as possible, and
- met consistent design criteria.
Learn more about the Effects of Tip Velocity on Rotor Designs
Sandia boasts more than 35 years of applied VAWT technology research. We now apply this knowledge base to modern, innovative design concepts such as the Floating VAWT, a design concept for accessing wind power in deep-water environments.
Learn about Sandia’s history in VAWT technology.
Contact
Chris Kelley, National Rotor Testbed
(505) 845-9036
clkell@sandia.gov