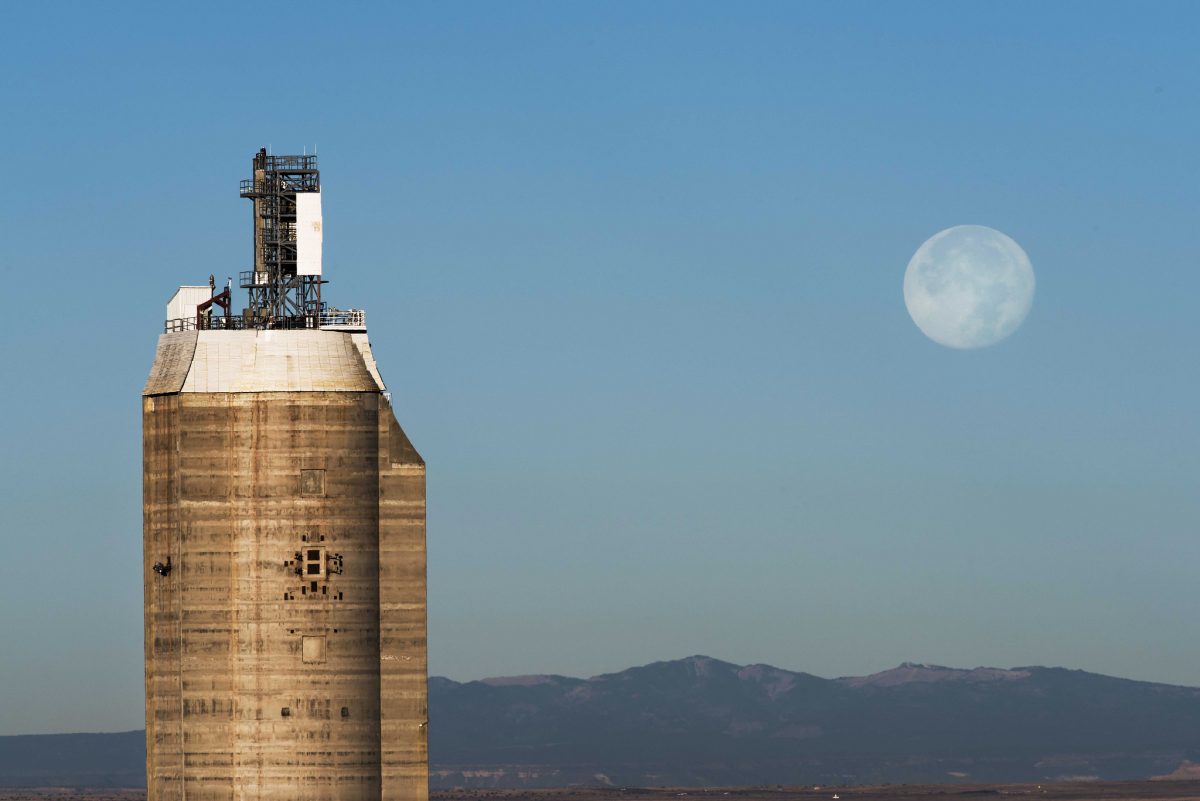
The CSP team uses SolidWorks software to research and develop all mechanical components for CSP systems.
On this page
Optical Tools | System Tools | Analysis Tools
Optical Tools
Solar Glare Analysis Tool
Availability
Due to new cybersecurity restrictions at Sandia, SGHAT is now available for internal Sandia use only. All external use of SGHAT is restricted, even by other government or military users. The glare tool source code and algorithms are available for licensing from Sandia Laboratories. Interested parties can contact the licensing department.
The licensed SGHAT applications are available for public use: ForgeSolar glare analysis tools at www.forgesolar.com If you have licensed SGHAT and would like to be listed, please contact us.
Solar Glare Hazard Analysis Tool
This tool determines when and where solar glare can occur throughout the year from a user-specified PV array as viewed from user-prescribed observation points. The potential ocular impact from the observed glare is also determined, along with a prediction of the annual energy production. Configurations can be quickly modified (e.g., tilt, orientation, shape, location) to identify a design that mitigates glare while maximizing energy production.
Meets FAA glare analysis requirements (78 FR 63276). SGHAT requires a modern web browser
Tower Illuminance Model
The Tower Illuminance Model (TIM) is a real-time interactive concentrating solar field simulation. TIM models a concentrating tower (receiver), heliostat field, and potential reflected glare, based on user-specified parameters such as field capacity, tower height and location. TIM provides a navigable 3D interface, allowing the user to “fly” around the field to determine the potential glare hazard from off-target heliostats. Various heliostat aiming strategies are available for specifying how heliostats behave when in standby mode. Strategies include annulus, point-per-group, up-aiming and single-point-focus. Additionally, TIM includes an avian path feature for approximating the irradiance and feather temperature of a bird flying through the field airspace.
Empirical Glare Analysis Tool
This tool allows the user to empirically quantify glint and glare from reflected light and assess the potential impact (e.g. temporary after-image, retinal burn). No expensive equipment is required. Simply upload photos of the glare and the sun.
Analytical Glare Estimation Tool
Analytically predict the potential impact (e.g. temporary after-image, retinal burn) of observed glare.
Phlux Mapping Analysis Tool
This tool allows the user to empirically determine the irradiance distribution on a central receiver. No flux gauge is needed. Simply upload photos and fill in the details, and the tool does the rest.
Reflectivity Calculator Tool
This tool allows the user to calculate the reflectivity of a receiver using only raw photos and details such as location and heliostat characteristics.
Infrared Signature Analysis Tool (IRSAT)
The software tool Infrared Signature Analysis Tool (IRSAT) was developed to enable users to evaluate the spectral irradiance from alternative systems at user-prescribed source temperatures and distances between the observer and source. The spectral irradiance profiles can then be analyzed for compatibility with optical sensors. In addition, computational fluid dynamics models have been developed to characterize vapor plumes generated from geothermal power plants.
Sandia Fringe Optical Analysis Slope Tool (SOFAST)
SOFAST is used to characterize the surface slope of reflective mirrors for solar applications. SOFAST uses a large monitor or projections screen to display fringe patterns, and a machine vision camera to image the reflection of these patterns in the subject mirror. From these images, a detailed map of surface normals can be generated and compared to design or fitted mirror shapes. SOFAST uses standard Fringe Reflection (Deflectometry) approaches to measure the mirror surface normals. SOFAST uses an extrinsic analysis of key points on the facet to locate the camera and monitor relative to the facet coordinate system. It then refines this position based on the measured surface slope and integrated shape of the mirror facet. The facet is placed into a reference frame such that key points on the facet match the design facet in orientation and position. This is key to evaluating a facet as suitable for a specific solar application. SOFAST reports the measurements of the facet as detailed surface normal location in a format suitable for ray tracing optical analysis codes. SOFAST also reports summary information as to the facet fitted shape (monomial) and error parameters. Useful plots of the error distribution are also presented.
Alignment Implementation for Manufacturing Using Fringe Analysis Slope Technique (AIMFAST)
The proper alignment of facets on a dish engine concentrated solar power system is critical to the performance of the system. These systems are generally highly concentrating to produce high temperatures for maximum thermal efficiency so there is little tolerance for poor optical alignment. Improper alignment can lead to poor performance and shortened life through excessively high flux on the receiver surfaces, imbalanced power on multicylinder engines, and intercept losses at the aperture. Alignment approaches used in the past are time consuming field operations, typically taking 4-6 h per dish with 40-80 facets on the dish. Production systems of faceted dishes will need rapid, accurate alignment implemented in a fraction of an hour. In this paper, we present an extension to our Sandia Optical Fringe Analysis Slope Technique mirror characterization system that will automatically acquire data, implement an alignment strategy, and provide real-time mirror angle corrections to actuators or labor beneath the dish. The Alignment Implementation for Manufacturing using Fringe Analysis Slope Technique (AIMFAST) has been implemented and tested at the prototype level. In this paper, we present the approach used in AIMFAST to rapidly characterize the dish system and provide near-real-time adjustment updates for each facet. The implemented approach can provide adjustment updates every 5 s, suitable for manual or automated adjustment of facets on a dish assembly line.
UFACET (Universal Field Assessment, Correction and Enhancement Tool)
UFACET is in development and funded by DOE SETO. UFACET will use unmanned aerial systems (UAS) and an imaging system payload to monitor optical errors in the heliostats while the heliostats are in operation or offline. UFACET can also be used to provide feedback during heliostat facet canting corrections.
Contact: Randy Brost
DelSOL
DelSOL is a performance and design code that includes optical and economic analyses. An analytical Hermite polynomial expansion/convolution-of-moments method is used to predict flux images from the heliostats in a computationally efficient manner (typically much faster than either MIRVAL or HELIOS). The code accounts for variations in insolation, cosine forshortening, shadowing and blocking, and spillage, along with atmospheric attenuation, mirror and receiver reflectivity, receiver radiation and convection, and piping losses. The code can be used to evaluate the system levelized energy cost and optimize the field layout, receiver dimensions, and tower height based on these costs. The code is written in FORTRAN77, and input to the code is entered via user-specified text files.
DELSOL3 source code, executable, and sample files
SOLERGY
SOLERGY simulates the operation and annual power output of a solar thermal power plant. It utilizes actual or simulated weather data at time intervals as short as three minutes and calculates the net electrical energy output including parasitic power requirements over a 24-hour day. Factors include energy losses in each component of the system, delays incurred during start-up, weather conditions, storage strategies, and power limitations for each component. The original version of SOLERGY (Stoddard et al., 1987) required that the energy collected by the receiver subsystem be sent to thermal storage. The code was later modified to allow the collected energy to bypass storage for analysis of the Solar One power plant (Alpert and Kolb, 1988). The code is written in FORTRAN77, and input to the code is entered via user-specified text files.
SOLERGY source code, executable, and sample files
System Tools
DelSOL
DelSOL is a performance and design code that includes optical and economic analyses. An analytical Hermite polynomial expansion/convolution-of-moments method is used to predict flux images from the heliostats in a computationally efficient manner (typically much faster than either MIRVAL or HELIOS). The code accounts for variations in insolation, cosine forshortening, shadowing and blocking, and spillage, along with atmospheric attenuation, mirror and receiver reflectivity, receiver radiation and convection, and piping losses. The code can be used to evaluate the system levelized energy cost and optimize the field layout, receiver dimensions, and tower height based on these costs. The code is written in FORTRAN77, and input to the code is entered via user-specified text files.
DELSOL3 source code, executable, and sample files
SOLERGY
SOLERGY simulates the operation and annual power output of a solar thermal power plant. It utilizes actual or simulated weather data at time intervals as short as 3 minutes and calculates the net electrical energy output including parasitic power requirements over a 24-hour day. Factors include energy losses in each component of the system, delays incurred during start-up, weather conditions, storage strategies, and power limitations for each component. The original version of SOLERGY (Stoddard et al., 1987) required that the energy collected by the receiver subsystem be sent to thermal storage. The code was later modified to allow the collected energy to bypass storage for analysis of the Solar One power plant (Alpert and Kolb, 1988). The code is written in FORTRAN77, and input to the code is entered via user-specified text files.
SOLERGY source code, executable, and sample files
SAM
System Advisor Mode
Sandia National Laboratories has collaborated with National Renewable Energy Laboratories (NREL) to include probabilistic analysis using the SAM system tool.
Analysis Tools
Computational Fluid Dynamics
ANSYS FLUID
- The CSP team uses the ANSYS Fluid software to research and develop flow processes related to CSP research.
- ANSYS FLUID
MFIX
- The CSP team uses the MFIX tool suite to research flow process and modeling of flow in CSP systems.
- MFIX
Solid Works Flow Simulation
- The CSP team uses the SWFS to design and simulate the flow process in their CSP systems.
- SWFS
Finite Elements Analysis
ANSYS Mechanical
- The CSP team uses this application to model and engineer mechanical components for CSP research.
- ANSYS Mechanical
SolidWorks Simulation
- The CSP team uses this simulation software to simulate and create mechanical components for CSP systems.
SIERRA
Sandia National Laboratories possess a High Performance Computing Platforms known as SIERRA. The CSP team uses the SIERRA platforms for higher fidelity thermal/mechanical simulations of the receiver, heat exchanger, and storage components of a CSP system.
In the same suite as SIERRA, Matlab software is included to perform image processing and modeling.
Due to cyber security restrictions, SIERRA is only for internal use for Sandia National Laboratories personnel.
Computer Aided Design
The CSP team uses SolidWorks software to research and develop all mechanical components for CSP systems.