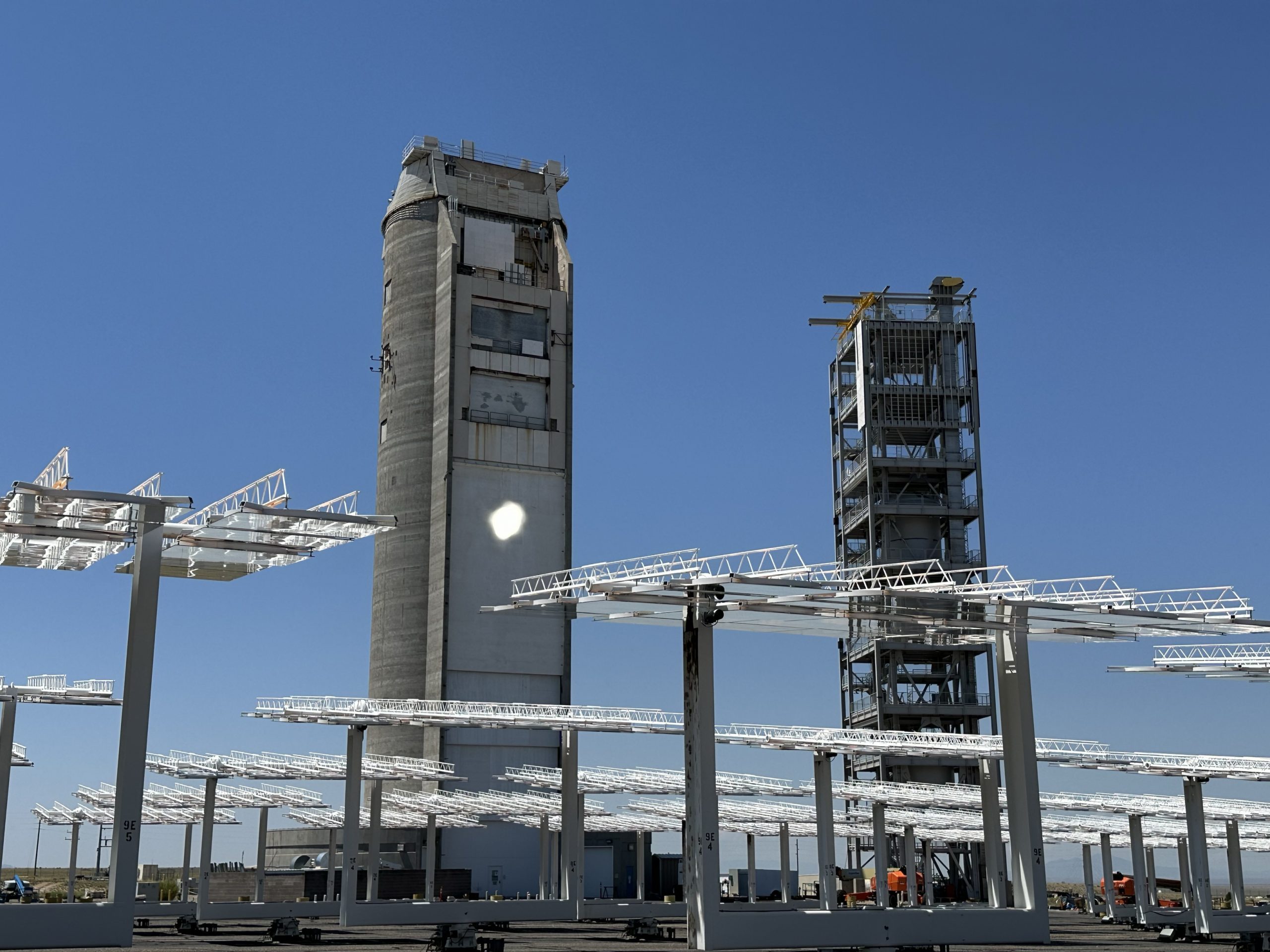
The National Solar Thermal Test Facility (NSTTF) is the only test facility of its kind in the United States, providing a range of high flux and extreme temperature capabilities using concentrated sunlight to support the development of renewable energy technologies and the next generation of materials.
What we can do
Our expertise includes Power Tower Systems, Advanced Falling Particle Technology, Thermal Energy Storage, High Flux Environments, and Precision Optics and Metrology.
Work with us
The NSTTF welcomes all users. Several mechanisms are available for non-Sandia researchers to contract with Sandia to use the facility. Previous users include government contractors and agencies, research institutes, universities, and private companies.