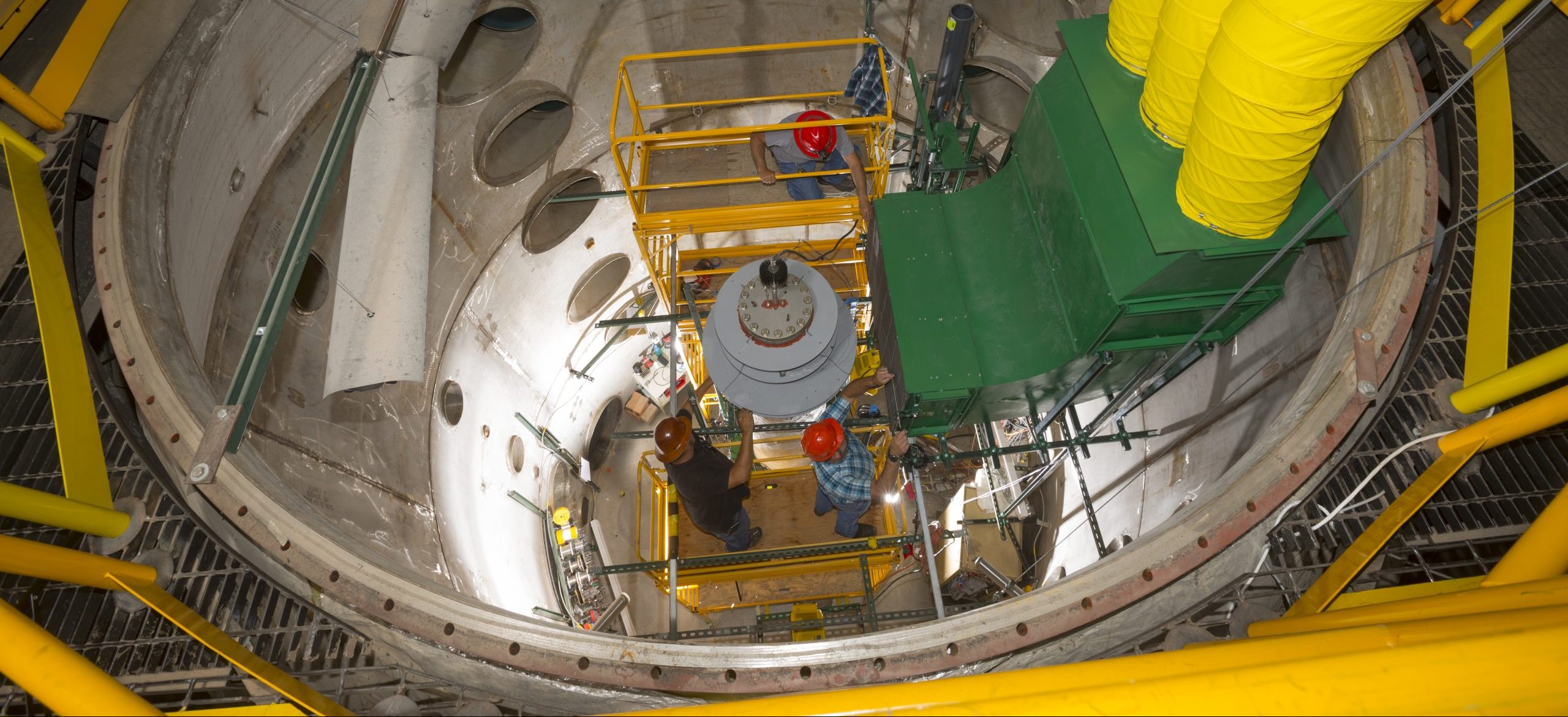
The U.S. inventory of spent nuclear fuel (SNF) from commercial nuclear power plants is estimated to reach approximately 135,000 metric tons by mid-century. Sandia performs research and development (R&D) to support the safe management and integration of the continued storage and transportation of commercial SNF, safeguards and security considerations, and the potential impacts from alternate/advanced fuel cycles.
We leverage state-of-the-art capabilities within the U.S. national lab complex, industry, academia, and international collaborators to provide experimental, analytical and modeling tools, data, and analyses to the U.S. government to make decisions and communicate the safety of long-term storage and subsequent transportation of SNF.
Sandia will continue to develop and perform cutting-edge testing and analysis to support an integrated solution to storage, transportation, and disposal challenges, with consideration of multiple clients and stakeholders.
Areas of focused research and development include:
- Storage research and development
- Transportation research and development
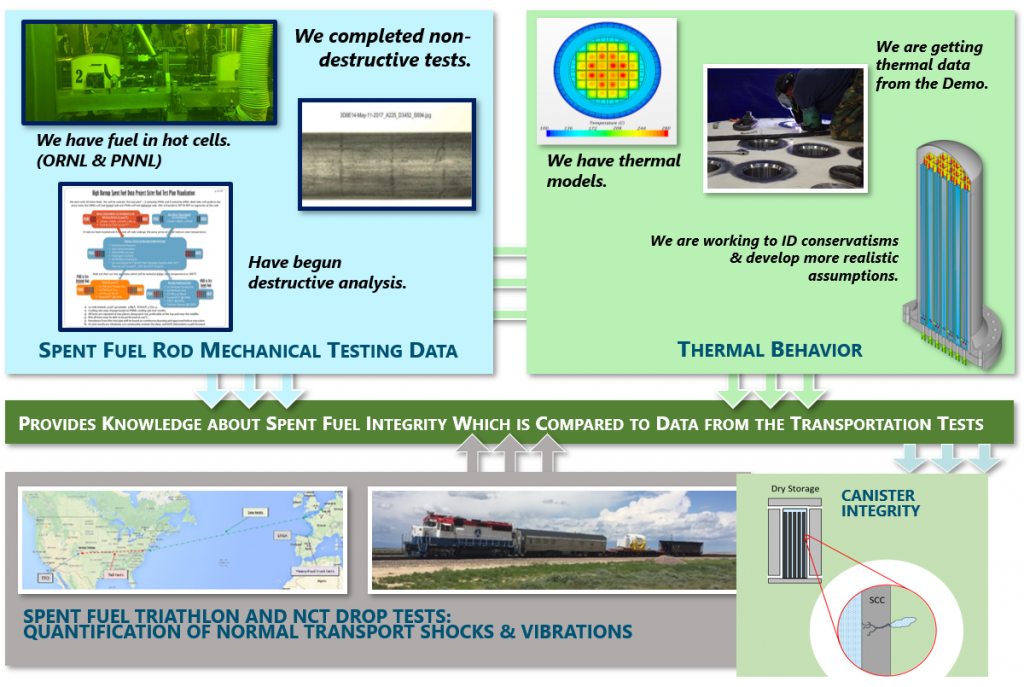
Storage Research and Development
Sandia’s storage R&D is focused on the performance and integrity of spent fuel and canisters in dry cask storage systems (DCSSs). We perform R&D to support the development of the technical basis for the extended storage and transportation of commercial SNF. The products are peer-reviewed research reports to be used by policy and regulatory decision makers.
Spent Fuel Integrity
Sandia, the U.S. Department of Energy (DOE), and the Electric Power Research Institute (EPRI) have a decades-long collaboration to obtain data on how SNF ages while in long-term storage. Data obtained from this collaboration is being used to develop aging management plans to mitigate potential changes to the spent fuel over time to better ensure that the fuel maintains its integrity for as long as needed.
Sandia plays a leadership role in the DOE/EPRI High Burnup Spent Fuel Confirmatory Data Project which has loaded and is storing a TN-32 dry cask with 32 high-burnup commercial spent fuel assemblies. This cask was loaded and is being stored using the same procedures and conditions that a typical cask would experience, except that 63 thermocouples were inserted into the cask to collect internal cask temperatures for at least ten years. After ten years of storage, it is planned that this cask will be opened, and the fuel rods will be examined to document changes in fuel integrity over years of storage. In the meantime, 25 spent fuel rods with similar make-up and burnup histories are being tested at PNNL, ORNL, and ANL to quantify and document the baseline mechanical integrity of these rods. Learnings to date show that temperatures within the cask did not ever get hot enough to cause radial hydride formation, the major cause of fuel embrittlement. Further, hot-cell and glove-box testing at PNNL, ORNL, and ANL, also has shown robust mechanical integrity.
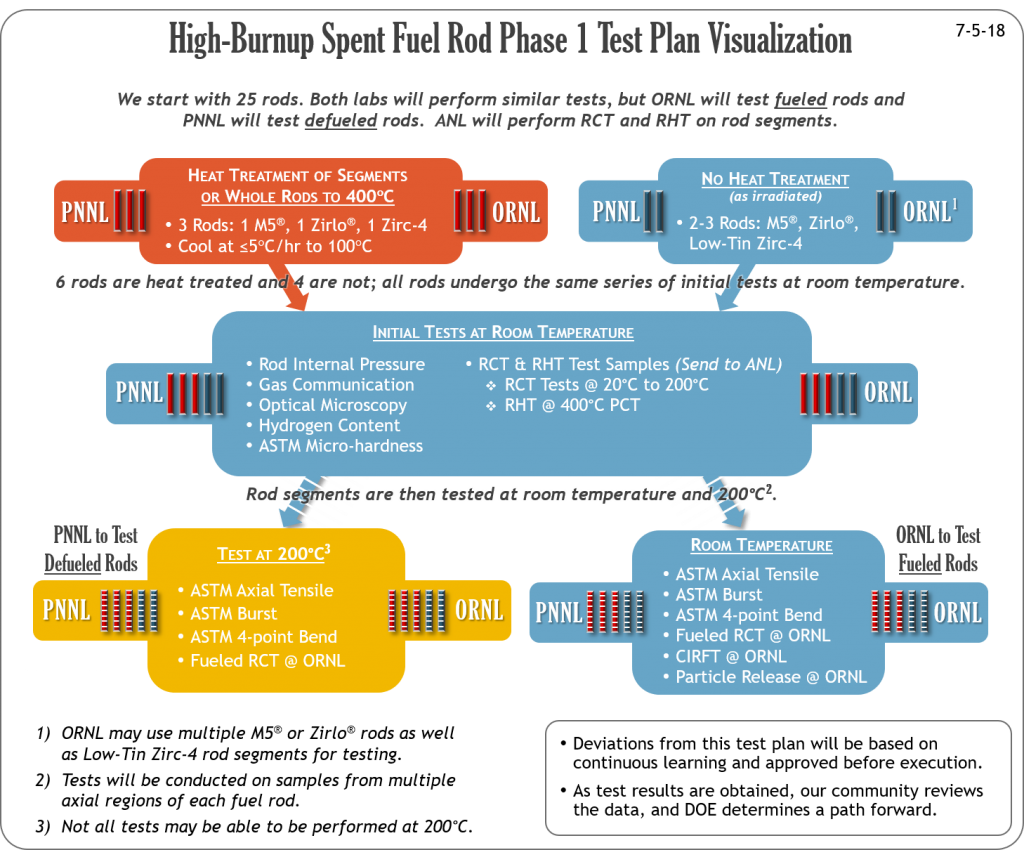
Storage System Integrity
Sandia performs R&D on stress corrosion cracking (SCC) of canisters in DCSS. Sandia’s R&D evaluates the three concurrent conditions required to cause stress corrosion cracking.
1. Susceptible Material
We are investigating the formation and effects of SCC by:
- Evaluating a stainless-steel canister’s internal stresses that may exist from the fabrication of the canister, particularly in and around welds and heat-affected zones, which are most susceptible to SCC
- Evaluating via sampling and analysis of dusts collected from the surface of in-service storage canisters, and by experimental testing of brine stabilities under canister surface conditions
- Evaluating typical weld samples
- Evaluating by characterizing weld residual stresses in a full diameter canister mockup, manufactured using identical procedures as in-service storage canister
2. Aggressive Environment
To test the effects of aggressive environments, several utilities provided dust samples from loaded canisters currently in service. Chloride salts, which can cause SCC, were found on canisters near the ocean. Sandia is in the process of collecting additional samples to determine:
- Deposited salt compositions
- Salt loads and compositions as a function of canister surface location and surface temperature
- How those salt compositions change in representative temperatures and humidities
- What environmental conditions are needed to support or stop corrosion and potential cracking
3. Tensile Stress
To evaluate tensile stress, which leads to expansion of materials, we used a full-diameter canister manufactured using identical procedures as in-service storage canister. Work is ongoing to understand incubation, pitting, transition from pit to crack, then crack growth rate, as well as what conditions lead to corrosion stifling. Also, monitoring and aging management practices at storage sites will be important to confirm storage system performance during extended service.
Thermal Hydraulic Experiments and Analysis of Dry Cask Systems
The Nuclear Energy Work Complex (NEWC) is comprised of two separate work sites, the CYlindrical BoiLing (CYBL) facility and the Surtsey test center. CYBL is an enclosed, three-story, climate-controlled building that can support open and confined space testing, such as dry storage system thermal-hydraulics and simulated cladding fires during spent fuel pool loss of coolant accidents. It is constructed around a robust stainless-steel tank that was originally built to test flooded reactor containment concepts. The Surtsey location includes large open areas for outdoor testing, smaller buildings for indoor testing, a blast pad for high-energy tests, and on-site facilities for developing test components (e.g., machining, electronics, fabrication, construction, videography, data acquisition). The NEWC facilities provide large-scale experimental capabilities focused on high-quality and real-world testing of nuclear power components, including prototypic spent fuel assemblies and dry storage systems. Conditions for testing include steady state and severe transients up to and including destruction of test assemblies. Testing at NEWC has supported technology development and addressed safety basis issues associated with extreme operating environments and postulated severe accidents for the DOE, NRC, and industry.
Commercial spent fuel dry storage systems utilize different drying cycles to remove water prior to storage. Given the lack of data suitable for the model validation of drying processes, carefully designed investigations that incorporate relevant physics and well-controlled boundary conditions are being developed to supplement existing field data. The insight gained through these investigations is expected to support the technical basis for the continued safe storage of SNF into long term operations.
DCSS for SNF are designed to provide a confinement barrier that prevents the release of radioactive material, maintain SNF in an inert environment, provide radiation shielding, and maintain subcritical conditions. The potential for stress corrosion cracks (SCCs) in canister walls is a concern for DCSS for SNF. Some of the canisters in these systems are backfilled to significant pressures to promote heat rejection via internal convection. This testing seeks to directly quantify the flow rate and aerosol transmission through engineered representations for SCCs under conditions of interest for SNF storage.
Temperature drives nearly all primary fuel degradation mechanisms under normal conditions. Therefore, accurate models are needed over a highly dynamic range of conditions to predict fuel performance. Current tests involve a dry storage cask simulator, which is instrumented with a geometrically prototypic BWR fuel assembly with heater rods to mimic the decay heat of spent nuclear fuel and is designed to validate various thermal-hydraulic codes, such as Ansys Fluent, STAR-CCM+, and COBRA SFS.
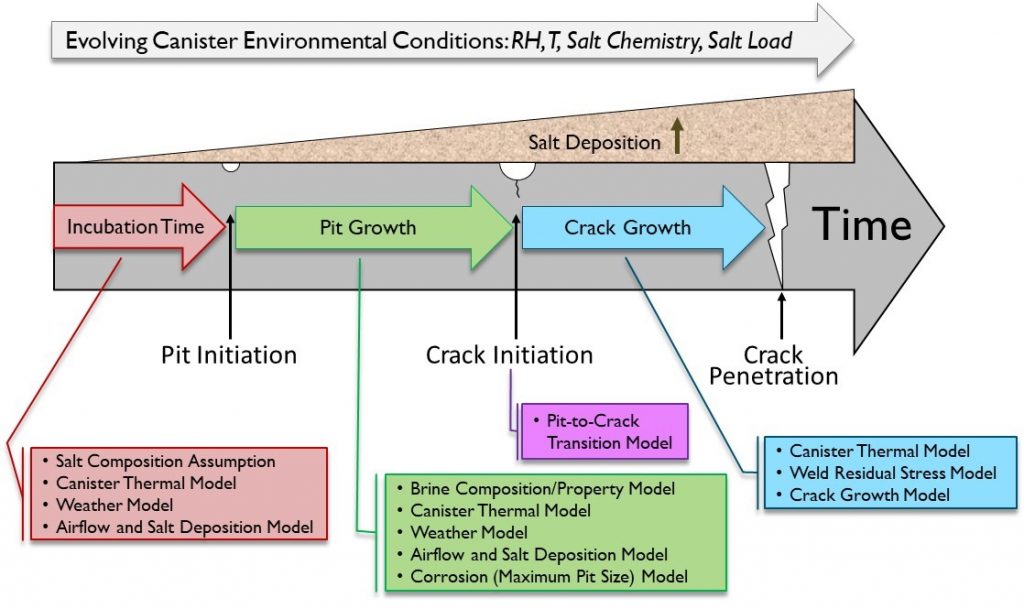
Transportation Research and Development
The U.S. inventory of SNF is currently stored at ~70 locations around the country. It must eventually be safely transported to a permanent disposal site and/or consolidated interim storage locations. Therefore, it is important to understand if and how transport could damage the spent fuel and/or storage canisters and transportation casks.
Sandia created and led an international team to evaluate safety implications of transporting spent nuclear fuel across the world. The team measured shocks and vibrations experienced by surrogate spent nuclear fuel during normal rail, barge, and truck transport using a highly instrumented storage/transportation cask. The analysis of the data collected revealed that the stresses the cladding experiences due to vibration and shock during transportation are far below yield and fatigue limits.
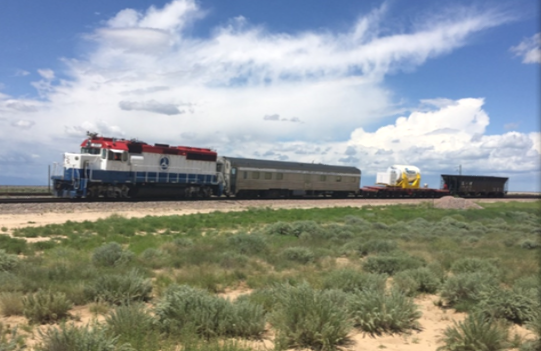
Contact
David Sassani
(505) 284-8967
dsassan@sandia.gov
Sylvia Saltzstein
(505) 844-0651
sjsaltz@sandia.gov
Emily Stein
(505) 845-0706
ergiamb@sandia.gov